우박 충격 테스트 지그를 개발한 이유
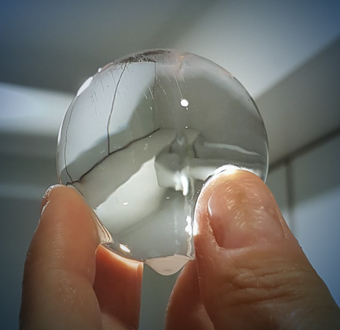
우박이 포함 된 뇌우와 같은 것들로부터 당신과 항공기를 보호하기 위해 현대 기술과 재료가 어떻게 개발되는지 궁금한 적이 있습니까? 복잡한 고장 메커니즘으로 인해 섬유 강화 복합 부품은 이러한 하중 사례에 대해 실험적으로 테스트해야 하며 때로는 예측할 수 없는 결과가 발생합니다.
예를 들어 Xycomp® DLF™ (불연속 장섬유)를 고려하십시오. 수년 동안 이 소재는 항공우주 응용 분야에서 복잡한 모양의 금속 부품을 대체할 수 있는 큰 가능성을 보여주었습니다. 불행히도, 매우 우수한 저속 (드롭 웨이트) 충격 거동과 충격 강도 후 압축의 낮은 녹다운에도 불구하고,이 재료의 고속 우박 충격 거동에 대한 불확실성이 초기에 제기되어 그러한 발생이 예상되는 위치에서 채택을 방해했습니다. 한 가지 적용 예로서, 이러한 부하 케이스는 충격 중에 방출된 모든 재료가 엔진에 의해 흡입되어 치명적인 결과를 초래할 수 있기 때문에 터보팬 엔진의 전면에서 특히 중요합니다. 따라서 DLF와 함께 중요한 부품을 개발하기 전에 DLF의 우박 충격 기능을 검증해야 했습니다.
테스트의 비용과 물류로 인해 우박 영향 데이터는 매우 제한적이었고 고객이 라미네이트 샘플에 대한 탐색 테스트를 수행한 한 경우에는 결과가 좋지 않았습니다.
이를 완전히 조사하기 위해 Greene Tweed의 첨단 기술 그룹은 고속 충격에서 DLF의 동작을 더 잘 이해하고 개선하는 것을 목표로 TD(기술 개발) 프로젝트를 시작했습니다. 테스트를 통해 저속 및 고속 충격 거동이 완전히 다르며 낙하 중량 테스트를 사용하여 우박 충격 성능을 예측할 수 없음을 확인한 후 테스트 기능이 핵심 구성 요소가 될 것이라는 것이 분명해졌습니다. 빠른 연구 반복 루프를 허용하는 테스트의 유연성이 프로젝트 성공의 주요 요인으로 확인되었지만 이러한 서비스를 제공하는 인정된 테스트 시설의 제한된 수, 테스트 비용 및 당시 팬데믹으로 인해 계속 확장되는 제한으로 인해 이러한 비전을 실현하기가 매우 어려웠습니다. 결과적으로 2020년 초에 내부 우박 충격 테스트 기능을 개발하기로 결정했습니다.
제한된 공간 내에서 200m/s 이상의 필요한 속도에 도달하는 방법을 결정하는 것부터 제한된 설치 공간 내에서 충격 속도를 정확하게 측정하는 방법을 찾는 것까지 많은 장애물을 극복해야 했습니다. 냉동실에서 발견되는 정상적인 "얼음 조각"이 외부에서 안쪽으로 굳어 심각한 내부 응력을 생성하여 가속 단계에서 우박이 부서져 장비를 그다지 유용하지 않은 스노우 캐논으로 만들기 때문에 우박 제조 과정 자체는 신중한 고려가 필요했습니다. 몇 가지 계획, 추가 테스트 및 몇 번의 반복 루프를 거쳐 테스트 기능이 완성되었고 실제 재료 조사가 시작될 수 있었습니다.
현재 구성에서 충격 테스트 지그에는 최대 600 x 500 x 300mm 크기의 부품을 최대 300m/s의 속도로 테스트할 수 있는 챔버가 있습니다. 테스트는 이미 2" 및 1.5" 직경의 우박으로 수행되었습니다. 테스트 관찰은 초당 10,000 프레임 이상을 기록 할 수있는 고속 카메라를 사용하여 수행됩니다.
Greene Tweed는 작년에 얻은 지식을 바탕으로 기존 연속 섬유 복합재의 고속 내충격성을 충족하거나 능가하는 새로운 DLF 재료 및 응용 설계 개념을 개발하고 시연할 수 있을 뿐만 아니라 불연속 복합재의 손상 거동을 더 잘 이해할 수 있었습니다. 현재 우박 충격 요구 사항이 있는 여러 항공 우주 응용 분야가 개발 중이며 내부 테스트 기능과 "교훈"을 잘 활용하고 있습니다.