Connecteurs scellés PAEK et verre-métal
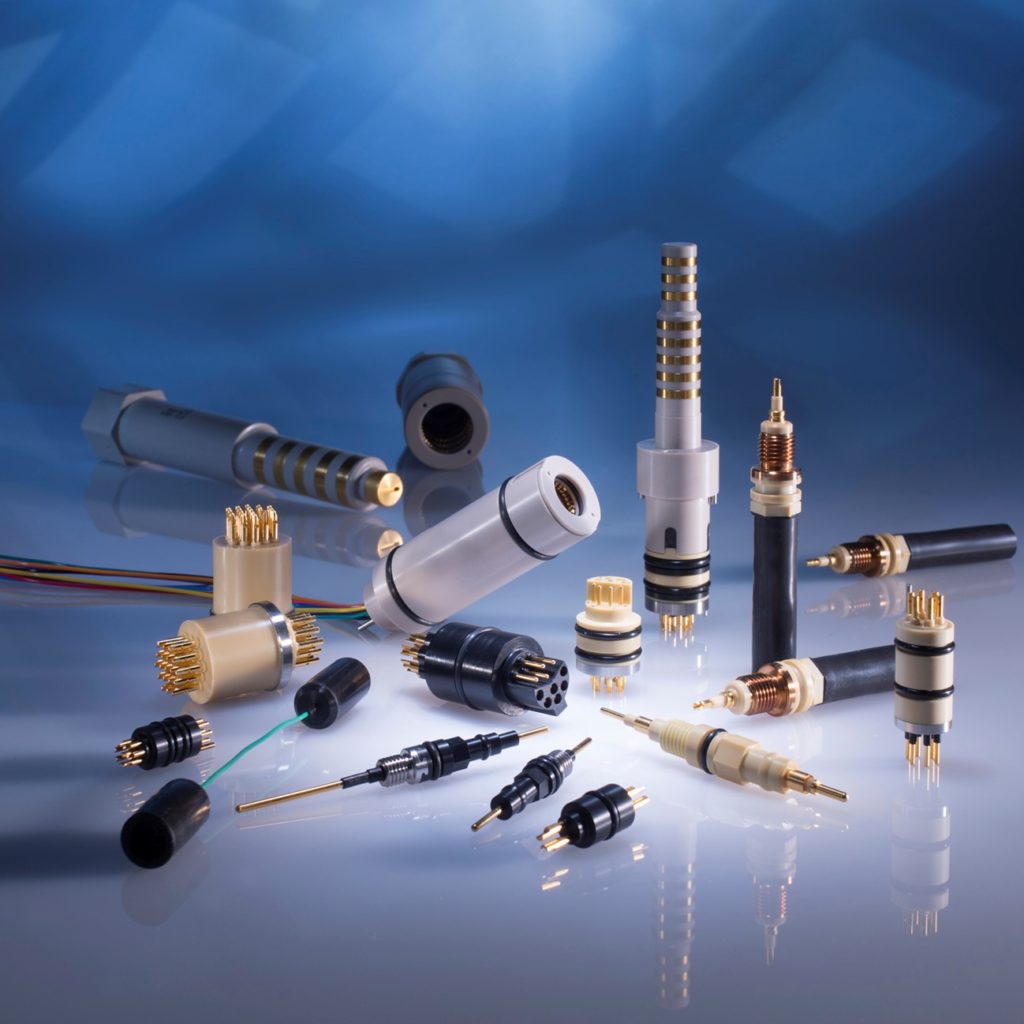
Si la méthode traditionnelle des connecteurs verre-métal (GTMS) constitue une barrière hermétique et un isolant électrique efficaces pour un large éventail d'applications médicales, automobiles, aérospatiales, militaires et géophysiques à basse pression, les thermoplastiques avancés développés au cours des trois dernières décennies se sont révélés être une solution supérieure pour les environnements de fonctionnement les plus extrêmes.
Dans la catégorie des thermoplastiques PAEK (polyaryléthercétone), un ensemble évolutif de nouveaux composés PEEK (polyéthercétone) et PEK (polyéthercétone) offre la stabilité thermique, la résistance mécanique, la faible usure, la résistance chimique, la résistance à l'isolation et la densité des broches requises pour les applications de connecteurs électriques les plus exigeantes, notamment les moteurs d'avion et les opérations de forage pétrolier et gazier HPHT (haute pression, haute température).
Scellement du verre
Depuis le XVIIe siècle, les joints verre-métal constituent des barrières étanches à l'air et ont été développés pour offrir une combinaison de scellement hermétique et d'isolation électrique. Dans un connecteur scellé verre-métal, le verre est fondu pour encapsuler à la fois la broche métallique et le boîtier afin de fournir une isolation conductrice entre le boîtier et les broches. Une couche d'oxyde visible est formée sur les composants métalliques, ce qui permet l'écoulement et l'adhésion du verre. La force du joint est limitée par la couche d'oxyde. Une étape supplémentaire est nécessaire au cours du processus de fabrication pour éliminer l'oxyde des autres surfaces du connecteur, ce qui risque d'entraîner une éventuelle contamination.
Le verre est un bon isolant électrique et il a une faible conductivité thermique, ainsi que la capacité de résister à une pression et une température de fonctionnement élevées. Toutefois, les limites des joints verre-métal deviennent évidentes lorsqu'ils sont soumis à des paramètres de fonctionnement extrêmes. Ces limites sont de deux ordres :
- Propriétés des matériaux du verre - Le verre est rigide et cassant, ce qui le rend susceptible de se fissurer sous l'effet de contraintes mécaniques dues à une pression élevée, à des chocs et à des vibrations, notamment en combinaison avec des cycles thermiques extrêmes.
- Contraintes du processus de fabrication - La difficulté de fondre le verre et sa viscosité à l'état fondu imposent des contraintes sur les types de métaux qui peuvent être utilisés.
Assortir le verre au métal
Les joints verre-métal sont formés par un processus de fusion à haute température, souvent supérieure à 900 °C, suivi d'un refroidissement rapide. La création d'un joint solide et résilient nécessite la correspondance du coefficient de dilatation thermique (CTE) entre le verre et les matériaux métalliques. Le CTE est la mesure dans laquelle un matériau se dilate et se contracte lorsqu'il est soumis à un changement de température. Pendant le processus de chauffage et de refroidissement, la vitesse à laquelle les changements de volume des deux matériaux doivent rester synchronisés, sinon des contraintes thermiques sont induites, car un matériau se dilate plus rapidement que l'autre.
En raison de la rigidité et de la fragilité inhérentes au verre, la gestion de tout décalage du CTE est essentielle pour éviter les tensions et les contraintes sur le joint qui peuvent entraîner des vides, une séparation entre le verre et le métal, ou une rupture de l'intégrité structurelle du verre. Le joint verre-métal doit non seulement survivre au processus de fusion pendant la fabrication, mais aussi aux milliers de cycles thermiques dans les conditions réelles de fonctionnement.
Cette exigence de correspondance du CTE du métal et du verre limite le choix du matériau métallique. Le kovar a été largement utilisé pour le conditionnement des joints verre-métal car la valeur de son coefficient de dilatation thermique linéaire de 5,5 × 10-6/K de 20 à 200 °C et de 4,9 × 10-6/K à 400 °C correspond étroitement au CTE du verre borosilicate. Les broches de traversée composées d'alliages de nickel et d'acier inoxydable sont également choisies pour leurs propriétés thermophysiques nécessaires. Cependant, ces matériaux impliquent des compromis significatifs en matière de conductivité électrique - l'objectif principal d'un connecteur électrique.
Le PEEK et le PEK répondent aux inconvénients du verre
L'introduction des connecteurs électriques en PEEK et PEK permet de surmonter les faiblesses inhérentes aux connecteurs verre-métal. Le coefficient de dilatation thermique du matériau thermoplastique n'a pas besoin de correspondre à celui du métal, ce qui permet d'optimiser les propriétés électriques des broches de traversée en métal. Sans la contrainte de faire correspondre les coefficients de dilatation thermique, les matériaux conducteurs peuvent être choisis en fonction de l'application plutôt que de la méthode de fabrication.
Par exemple, on peut utiliser du cuivre au béryllium (BeCu) qui offre une résistance électrique plus faible que l'Inconel et l'acier inoxydable. Cette conductivité plus efficace permet de faire passer plus de courant tout en générant moins de chaleur. Cela signifie une transmission plus fiable de l'énergie et des signaux.
Grâce à une conductivité électrique plus élevée, il est possible de réduire le diamètre des broches, ce qui permet une densité de broches nettement plus élevée et une plus grande souplesse dans la conception du motif des broches, d'où une réduction de la taille globale du connecteur. Les procédés de moulage par injection avec des plastiques sont également mieux adaptés à la fabrication de très petites pièces que le procédé de fusion du verre. Le matériau thermoplastique plus léger, combiné à la taille réduite des broches et du connecteur dans son ensemble, permet une réduction significative du poids par rapport aux connecteurs GTMS. Avec des applications dans les secteurs de l'aérospatiale, du sous-marin et de l'énergie, le poids et les dimensions des composants sont essentiels aux performances globales du sous-système.
Une différence importante entre le PEEK et le verre est la géométrie du joint interne, où le matériau isolant encapsule chaque broche métallique. Les connecteurs en PEEK sont fabriqués par un procédé de moulage par injection dans lequel le PEEK est surmoulé sur la broche. Grâce à cette méthode, le joint s'étend sur toute la longueur de la broche métallique. Par conséquent, le lien est plus durable que les joints en verre rigide. Les contraintes internes dans les joints en verre ou l'expansion thermique inégale du contact métallique peuvent provoquer des fissures dans la surface d'étanchéité, ce qui entraîne une défaillance prématurée de la pièce. La température de transition vitreuse plus basse du PEEK permet une légère déformation sous l'effet de la pression ou des vibrations. En surmoulant les contacts métalliques, le connecteur tolère un léger désalignement de l'accouplement et est moins sensible aux mauvaises manipulations pendant l'installation et aux dommages dus aux chocs mécaniques. Les broches déformées peuvent être réalignées sans qu'il soit nécessaire de jeter la pièce.
Les applications les plus exigeantes
Dans les applications où la fiabilité et la constance des performances sont essentielles, comme les moteurs d'avion et les opérations de forage en profondeur, les connecteurs électriques en PEEK et PEK offrent plusieurs avantages importants :
- Transmission fiable de l'énergie et des signaux - Compatibilité avec le matériau optimal des broches métalliques, comme le cuivre au béryllium.
- Applications HPHT - Jusqu'à 232°C (450°F) et jusqu'à 35 000 psi, et avec le thermoplastique PEEK réticulé avancé spécialisé, jusqu'à 260°C (500°F) et 45 000 psi. Résilience aux cycles rapides et extrêmes de pression et de température
- Résilience chimique - Sulfure d'hydrogène, méthanol, fluides de forage, produits de puits, etc.
- Résistance mécanique - Résilience aux chocs et aux vibrations sans perte de continuité
- Durabilité - Moins sensible aux dommages causés par une mauvaise manipulation.

Les thermoplastiques sont plus performants que le verre
Le PEEK et le PEK surmontent les limites du verre pour offrir des performances supérieures dans les conditions de fonctionnement les plus exigeantes. Les propriétés des matériaux thermoplastiques surmontent la rigidité et la fragilité du verre pour offrir une bien meilleure résistance aux contraintes mécaniques de la pression, des chocs et des vibrations. Le processus de fabrication des connecteurs thermoplastiques permet l'utilisation de métaux à faible résistance électrique pour des performances de transmission de puissance et de signaux nettement supérieures.
Les ingénieurs et les chercheurs continuent de développer des matériaux élastomères et thermoplastiques innovants pour améliorer la fiabilité et les performances. En plus du PEEK non chargé, les connecteurs électriques sont disponibles en PEK non chargé pour des propriétés thermophysiques améliorées, ainsi qu'en grades chargés de PEEK et PEK pour une meilleure résistance mécanique. Pour les conditions extrêmes, le PEEK réticulé, tel que l'Arlon 3000XT®, peut fonctionner à des températures allant jusqu'à 500 °F, à des pressions de 45 000 psi, et s'est avéré être 30 % plus résistant que d'autres matériaux utilisés dans l'exploration pétrolière et gazière.
Cet article est tiré du nouveau livre électronique "Connector Supplier", 2022 Rugged Interconnects for Harsh Environments.