Comment augmenter la fiabilité et la durée de vie des pompes dans les services d'OT ?
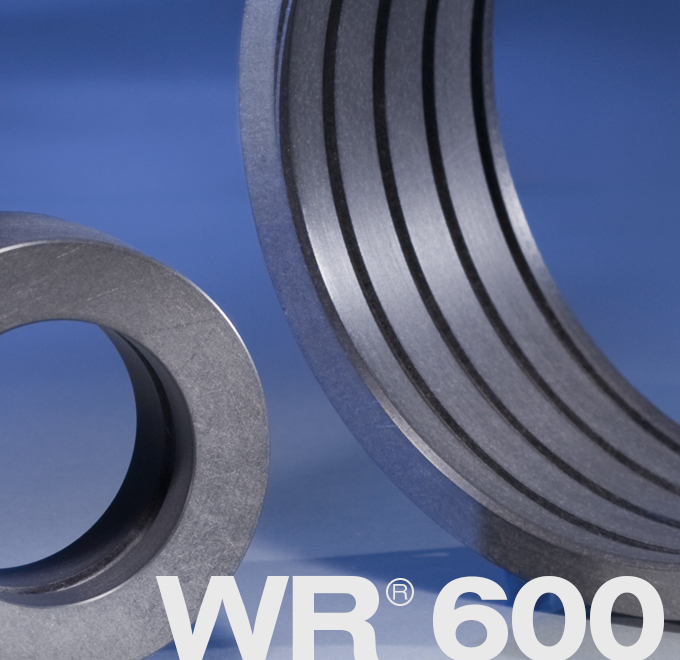
Ceci est le deuxième article d'une série sur les défis de l'oxyde d'éthylène. Lire la première partie
Les entreprises qui fabriquent ou travaillent avec de l'oxyde d'éthylène (OE) savent que plusieurs défis sont associés à ce composant chimique essentiel : son inflammabilité, sa réactivité, sa décomposition en vapeurs explosives et sa toxicité. C'est pourquoi il est impératif d'utiliser des équipements, y compris tous leurs composants et matériaux, qui sont compatibles avec l'OE.
La pompe est l'une de ces pièces d'équipement essentielles. Il est essentiel de spécifier les matériaux appropriés pour les composants de la pompe, tels que les roulements et les joints, lorsque des produits chimiques hautement agressifs comme l'OE sont en jeu. La sélection de matériaux qui ne sont pas compatibles avec l'OE peut entraîner des opérations peu fiables et dangereuses. Cela peut entraîner une perte potentielle de production et, pire encore, de vies humaines.
Éliminer les problèmes de gonflement des roulements et améliorer l'efficacité de la pompe
En raison de la nature explosive de l'oxyde d'éthylène et des problèmes de sécurité qu'il pose, plusieurs fabricants de produits chimiques utilisent des pompes à rotor noyé sans garniture conçues sur mesure. Les milieux chimiquement agressifs, tels que l'OE, peuvent attaquer les matériaux traditionnels des roulements et des joints.
C'est ce qui s'est passé dans une importante usine de traitement chimique en Allemagne qui produit de l'OE. Cette entreprise de produits chimiques spéciaux utilise des pompes à rotor noyé fabriquées par HERMETIC-Pumpen GmbH, connues pour leurs pompes sûres et durables dans les applications les plus extrêmes et dans les milieux pompés les plus dangereux. Ces pompes contenaient des bagues d'usure en PEEK remplies de fibres de carbone qui gonflaient dans le milieu EO. Le gonflement excessif des bagues d'usure entraînait un fonctionnement peu fiable de la pompe, réduisant le temps moyen entre les défaillances (MTBF) à un mois et parfois une semaine.
Ils ont contacté Greene Tweed à la recherche d'un nouveau matériau pour les bagues d'usure afin de faire face aux conditions de traitement difficiles du service d'OE. Nous avons recommandé de remplacer les bagues d'usure en PEEK remplies de carbone par des paliers WR®600, un composite à base de PFA renforcé de fibres de carbone dont la température maximale de service continu est de 260°C (500°F). Sa résistance chimique exceptionnelle est due à ses composants, qui peuvent supporter pratiquement tous les environnements, y compris les acides, les bases, les halogènes et les solvants les plus puissants. Le WR®600 est un matériau composite qui ne se gorge pas et ne se colle pas, ce qui permet aux bagues d'usure d'être conçues avec des jeux serrés, d'où une efficacité accrue et une durée de vie plus longue. En remplaçant les bagues d'usure de la pompe par du WR600, l'usine chimique a augmenté son MTBF de quelques semaines à plus de deux ans. Encouragée par ces résultats, l'usine chimique a spécifié le WR® 600 pour toutes les pompes Hermetic sur site en service EO.
Prolonger la durée de vie des joints
Dans les usines chimiques qui utilisent des pompes à garnitures mécaniques, l'OE est l'un des produits chimiques les plus agressifs. Il peut faire gonfler la plupart des matériaux d'étanchéité, entraînant la défaillance du joint dans un délai très court. La sélection d'un élastomère perfluoré, également connu sous le nom de FFKM, optimisé pour les applications d'OE, peut réduire le risque de défaillance de l'équipement.
Une grande entreprise chimique située dans l'est de l'Allemagne a connu des défaillances répétées de plusieurs FFKM en raison de l'exposition à l'OE. Il en résultait une maintenance non planifiée de leurs pompes à vis sans fin toutes les quelques semaines. L'entreprise a contacté Greene Tweed pour l'aider à augmenter le MTBF de ses pompes de quelques semaines à plusieurs années, tout en améliorant la sécurité de toutes les installations de pompes.
Après une évaluation minutieuse de l'application et de ses paramètres de fonctionnement, nous avons proposé Chemraz® 505, un FFKM qui offre une large gamme de résistance chimique. Après avoir testé avec succès Chemraz® 505 dans une usine pilote de service d'OE de R&D, la société chimique a spécifié Chemraz® 505 pour toutes les pompes à vis sans fin de l'usine.
Il ne fait aucun doute qu'il est essentiel pour les entreprises chimiques travaillant avec l'OT de choisir des matériaux appropriés pour leurs applications. En choisissant les roulements WR®600 pour leurs pompes à rotor noyé et les joints Chemraz® 505 pour les pompes rotatives, les usines chimiques en service EO peuvent :
Références :
1https://en.wikipedia.org/wiki/Chemical_Industries_of_Ethylene_Oxide_explosion
2https://www.osha.gov/pls/imis/accidentsearch.accident_detail?id=201146065