How to Increase Reliability and Pump Lifetime in EO service
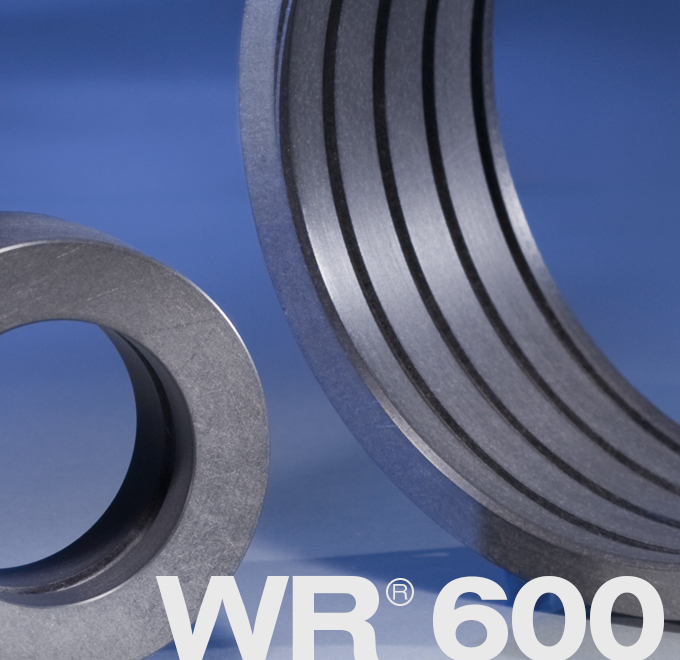
This is the second article in a series on Ethylene Oxide Challenges. Read Part 1
Companies that manufacture or work with Ethylene Oxide (EO) know that there are several challenges associated with the essential chemical building block – its flammability, reactivity, explosive vapor decomposability, and toxicity. That is why it is imperative to use equipment, including all of its components and materials, that are compatible with EO.
One such critical piece of equipment is the pump. Specifying the proper materials for pump components, such as bearings and seals, is critical when highly aggressive chemicals such as EO are a factor. Selection of materials that are not compatible with EO can lead to unreliable and unsafe operations. This could lead to potential loss of production and even worse, lives.
Eliminate Bearing Swell Issues and Improve Pump Efficiency
Due to the explosive nature and critical safety concerns with EO, several chemical manufacturers utilize custom designed sealless, canned-motor pumps. Chemically aggressive media, such as EO can attack traditional bearing and seal materials.
That was the case at a major chemical processing plant in Germany that produces EO. The specialty chemicals’ company uses canned motor pumps produced by HERMETIC-Pumpen GmbH, known for their safe and durable pumps under the most extreme applications and in the most hazardous pumped media. These pumps contained carbon-fiber filled PEEK wear rings that were swelling in EO media. The excessive swelling of the wear rings resulted in unreliable pump operation, reducing Mean Time Between Failures (MTBF) to a month and sometimes a week.
They reached out to Greene Tweed in search of a new wear rings material to handle the harsh processing conditions of the EO service. We recommended replacing the carbon-filled PEEK wear rings with WR®600 bearings, a carbon-fiber-reinforced, PFA-based composite with a maximum continuous service temperature of 500°F (260°C). Its outstanding chemical resistance comes from its constituents, which can withstand virtually all environments, including the strongest acids, bases, halogens, and solvents. WR®600 is a non-galling/non-seizing composite material, which allows the wear rings to be designed with tight clearances, leading to improved efficiency and longer life. As a result of changing the pump wear rings to WR600, the chemical plant extended their MTBF from a few weeks to over two years and counting. Encouraged by the results, the chemical plant has specified WR® 600 on all onsite Hermetic pumps in EO service.
Extend Seal Life
At chemical plants that utilize pumps with mechanical seals, EO is one of the most aggressive chemicals. It can swell most seal materials, causing the seal to fail within a very short time. Selecting a perfluoroelastomer, also known as FFKM, optimized for EO applications, could reduce the possibility of equipment failure.
A leading chemical company located in Eastern Germany experienced repeated failure of multiple FFKMs due to EO exposure. This resulted in unplanned maintenance of their screw spindle pumps every few weeks. They contacted Greene Tweed to help increase the MTBF of their pumps from several weeks to several years, while improving safety at all pump installations.
Following a careful evaluation of the application and its operating parameters, we proposed Chemraz® 505, an FFKM that provides a wide range of chemical resistance. After successfully trialing Chemraz® 505 in an R&D pilot EO service plant, the chemical company specified Chemraz® 505 for all screw spindle pumps throughout the plant.
Undoubtedly, it is critical for chemical companies working with EO to choose appropriate materials for their applications. By choosing WR®600 bearings for their canned pumps and Chemraz® 505 seals for rotary pumps, chemical plants in EO service can:
References:
1https://en.wikipedia.org/wiki/Chemical_Industries_of_Ethylene_Oxide_explosion
2https://www.osha.gov/pls/imis/accidentsearch.accident_detail?id=201146065