シールの相手金具の正しい表面仕上げを知っていますか?
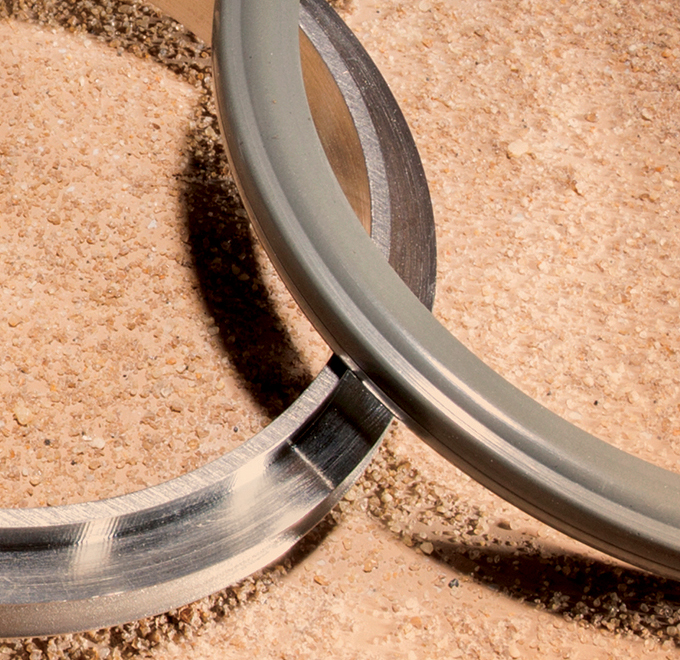
お使いの機器のシーリングシステムが早期に故障したり、正しく機能していないことを想像してみてください。シールに欠陥があるのか、シール材が温度や圧力の要求に耐えられないのか、すぐに確認したいと思うかもしれません。また、サイズが適切かどうか、スクイーズレベルを確認したいと思うかもしれません。
しかし、相手方のハードウェアについてはどうでしょうか?ハードウェア設計のいくつかの側面は、シールが適切に機能するかどうかを左右し、シーリングエレメントの動的寿命に影響を与える可能性があります。理想的な表面仕上げはシーリング性能を決定し、シーリングエレメントの寿命を最大化することができるため、相手側金具の表面仕上げ(シールを圧縮する2つの面の粗さ)は設計時に考慮すべき要因の1つである。
表面仕上げの条件は、シールがエラストマーか熱可塑性樹脂か、あるいは他の材料かによって異なる。エラストマーは全体的に可鍛性であるため、表面仕上げの適合性が高く、一方、より硬い熱可塑性プラスチックは適合性が低いものの、そのトライボロジー特性により潤滑が少なくて済むことがあります。そのため、熱可塑性樹脂シールの表面仕上げは、一般的にエラストマーシールよりも細かい仕上げを推奨しています。
また、液体をシールする用途と気体や真空をシールする用途では、表面仕上げの要件が異なる。気体や真空をシールする場合は、気体の構造と大きさによって、液体が通るよりも小さな隙間を通ることができるため、より細かい表面仕上げが推奨される。
動的なアプリケーションでは、ハードウェアの表面仕上げもシールの寿命に直接影響します。摩擦を減らすために、プロセス媒体や潤滑液を表面に捕捉するために、ハードウェアの表面にばらつきがあることが必要です。しかし、表面が粗すぎると、シールエレメントがハードウェアと接触することで磨耗してしまいます。潤滑とシールの寿命を両立させるためには、適切なバランスを見つけることが非常に重要です。
下図は、一般的な表面粗さの測定方法を示す、表面の高さと粗さの局所的なばらつきの描写である。図左のような山が多すぎると、シール材が動的接触により摩耗することはもちろん、局所的な表面高さのばらつきに対応しきれないことは容易に想像できる。また、図の右側の谷の部分にはポケットが形成され、プロセス媒体や潤滑剤を閉じ込めることができ、連続的な動的サイクルによる摩擦を減少させることができることが示されている。
お客様のアプリケーションのハードウェア部品に適した表面仕上げを選択することは、複雑な場合があります。一般的に、動的シールには8~12μinches Ra(平均粗さ)、静的シールには16~32μinches Raを推奨しています。グリーンツイードの経験豊富なエンジニアが、お客様のアプリケーションのパラメータにアクセスし、適切な表面仕上げを導き出すお手伝いをいたします。