About Us
Over 160 years of science, engineering, and innovation
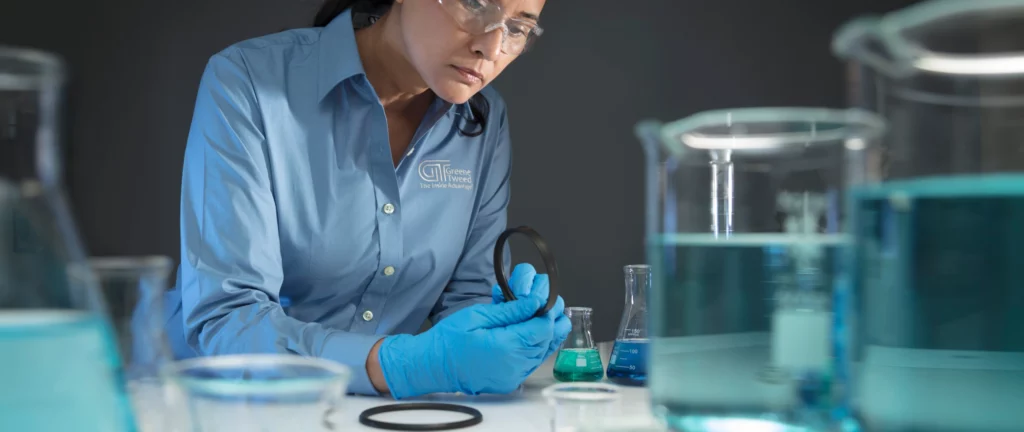
WHAT WE DO
Greene Tweed designs and manufactures components, materials, and solutions that perform in the harshest environments. We engineer for conditions where equipment failure is not an option. Our products are made for extreme temperatures, pressure, chemical corrosion, and mechanical wear.
With over 200 engineers in labs throughout North America, Europe, and Asia serving a variety of industries, we work with you to create a customized solution tailored to your critical operations’ requirements.
Greene Tweed technical experts are always innovating, researching, and developing new thermoplastics, composites, and customized components. We are dedicated to expanding our clients’ performance in the world’s harshest environments.
Mission Statement
To enable customers to operate efficiently and safely in the world’s most demanding environments; we design, manufacture, and deliver innovative products with trusted performance for markets where failure is not an option.
Vision
To be a trusted technology leader and market-driven organization that delivers value and innovation in everything we do. We will continue to grow profitably at rates exceeding benchmarks in the industries we serve.