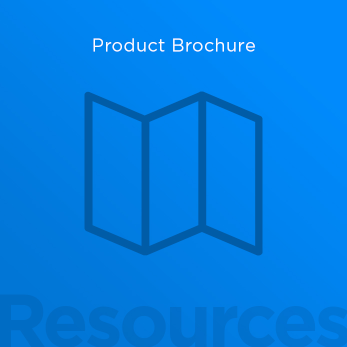
Product Details
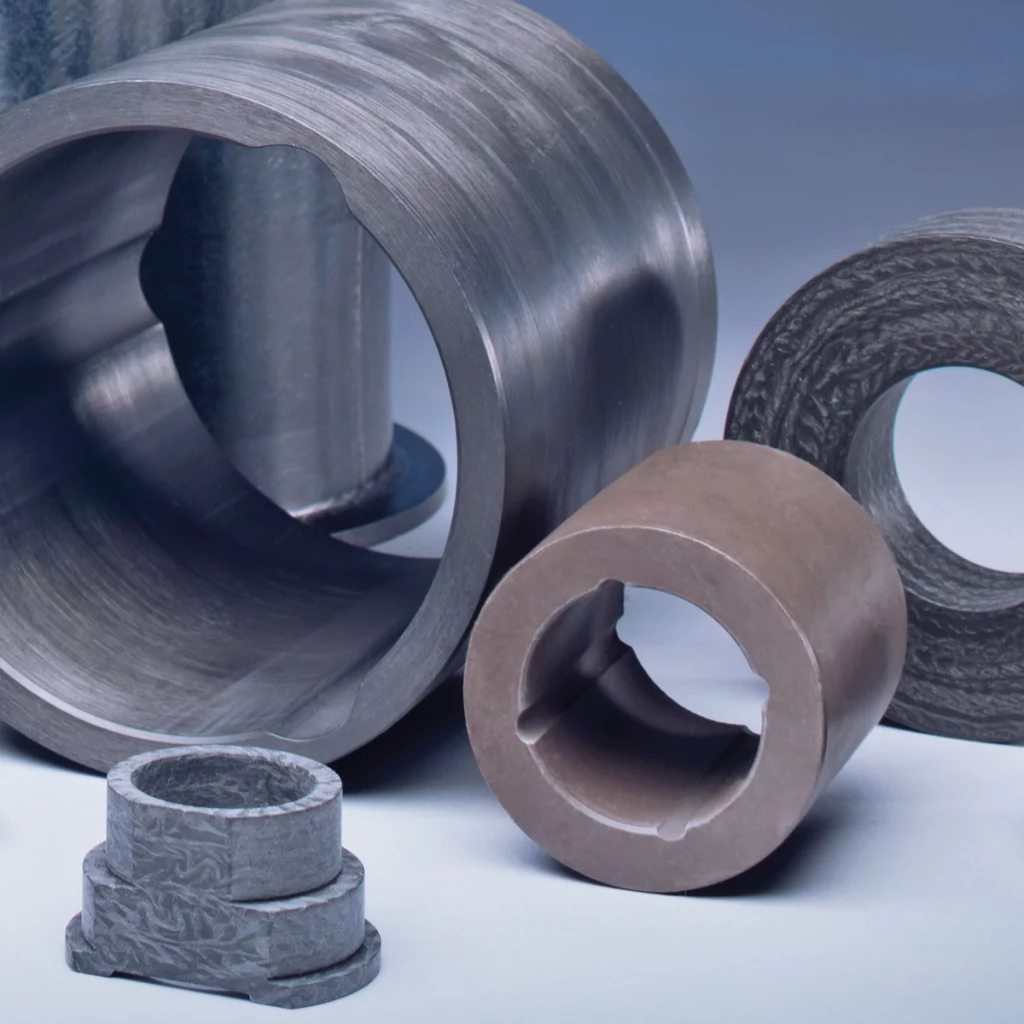
WR® & AR® Pump & Compressor Wear Parts
Greene Tweed thermoplastic composite wear parts are designed to enhance the safety and efficiency of your operations. Lighter and more resistant than their metal counterparts, our engineered components have become the industry standard for refineries, chemical plants, and power generation plants.
The non-galling, non-seizing performance and chemical resistance of WR® (Wear Resistant) composites cut down wear and friction. AR® (Abrasion Resistant) composites reduce downtime for pumps handling media-containing solids. All composites are built to withstand even your most extreme applications and volatile environments.
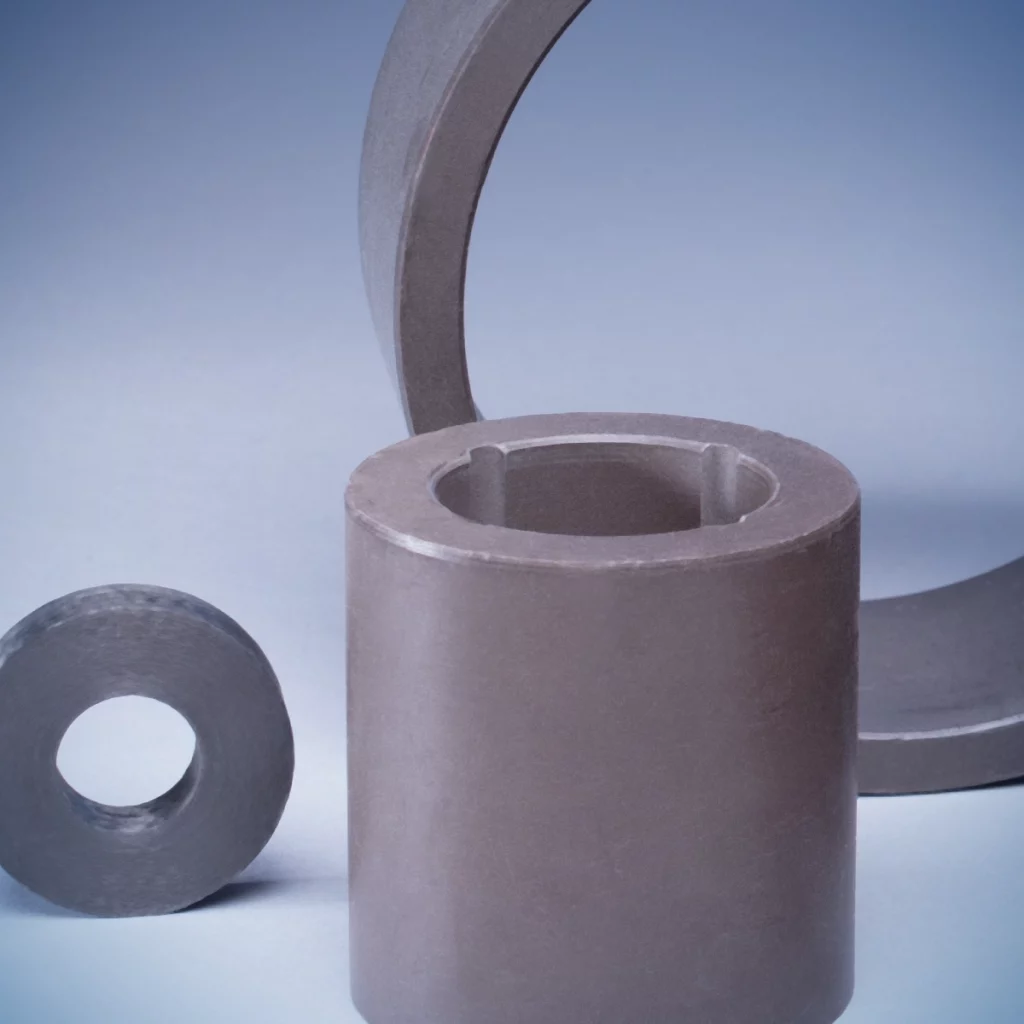
Features and Benefits
- Reduced repair and maintenance time
- Minimized chance of damage to critical components
- Reduced vibration due to tighter clearance
- Resistant to extreme temperatures and corrosion
- Improved reliability and efficiency of older equipment
Industries & Applications
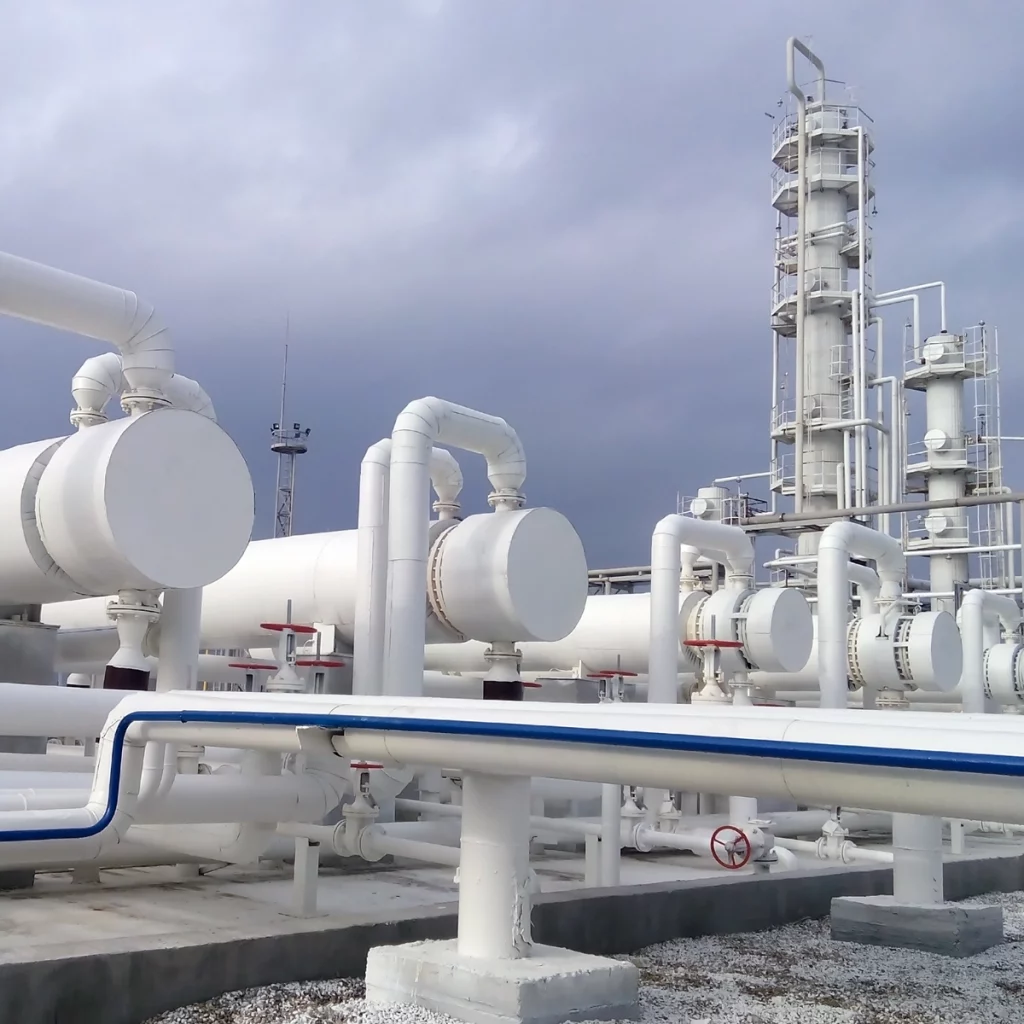
Avoid Damage and Downtime
Greene Tweed engineered components are custom designed to be used for your most challenging applications. No matter how demanding the environment, our team works with you to determine the right solution for the job.
Applications include:
- Turbines
- Pumps
- Compressors
- Wear rings
- Refining
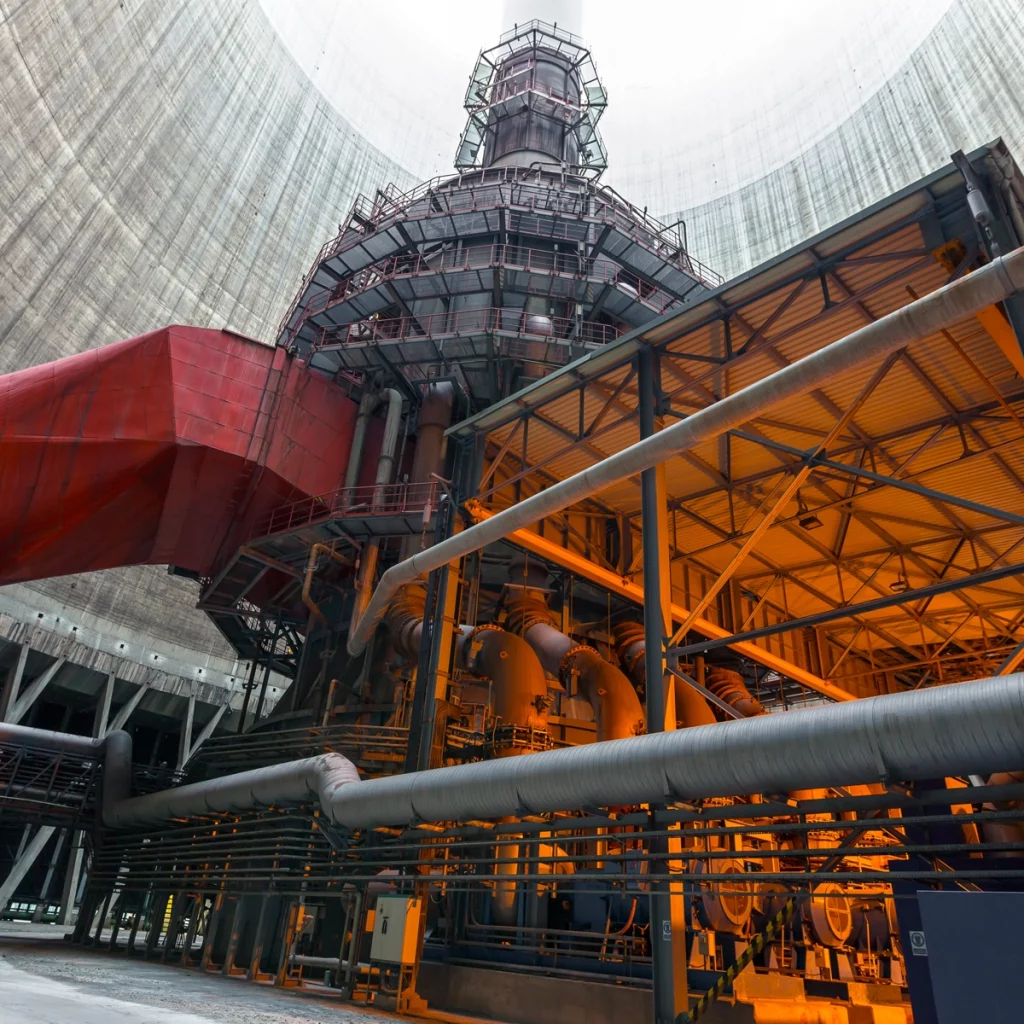
Reliable Performance
Greene Tweed engineered components are custom designed to be used for your most challenging applications. No matter how demanding the environment, our team works with you to determine the right solution for the job.
Applications include:
- Bearings
- Bushings
- Thrust bearings
- Wear rings
- Flow restriction/rotor support
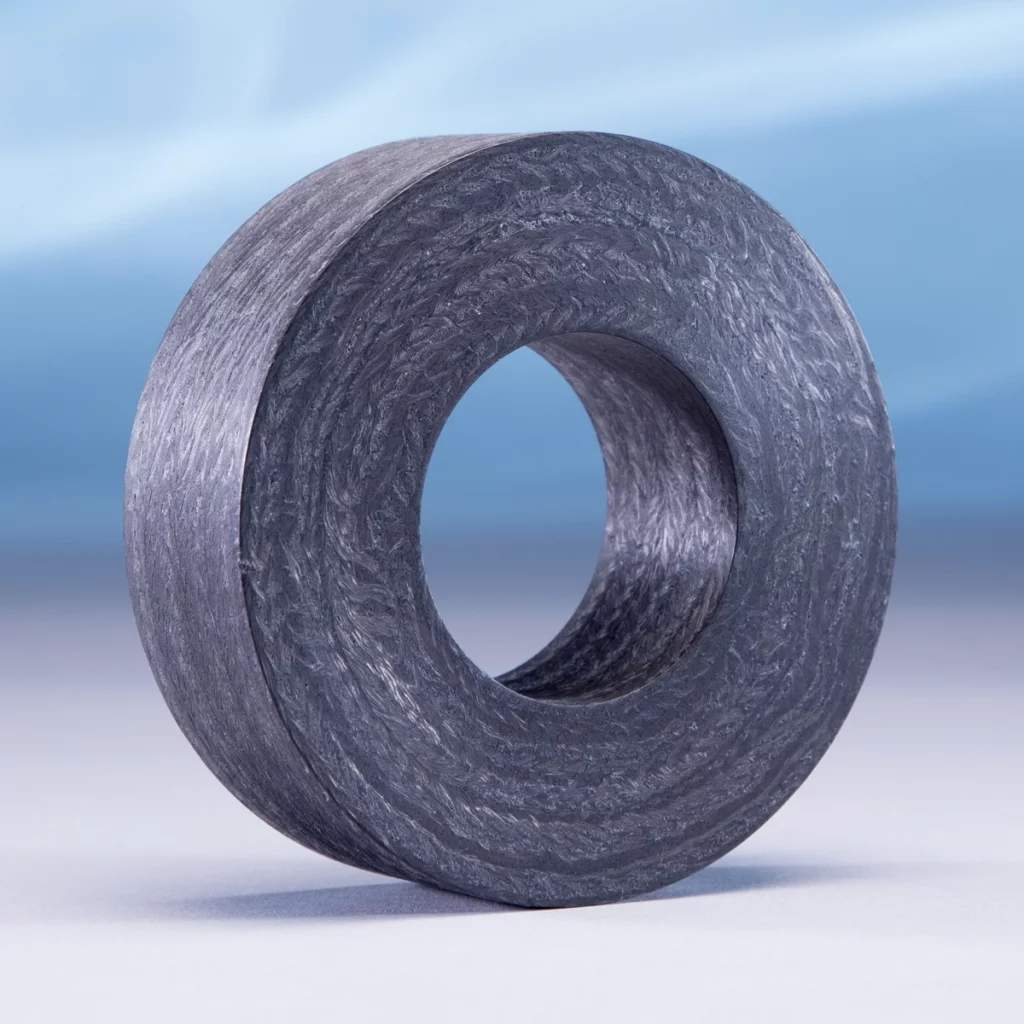
WR® 650 Wear Ring
High-Efficiency Centrifugal Pump Solution
One of the biggest chemical plant operators in Southeast Asia came to us with a challenge. Their existing centrifugal dryer circulation pump was an older model without a wear ring, and it needed an upgrade.
Looking for a cost effective solution to increase pump efficiency, they installed a Greene Tweed WR®650 wear ring. Internal loss and leakage decreased. Pump performance increased. The upgrade improved discharge pressure, power derived from increased flow, and pump capacity.
Results from a commission test proved that the pump was 9% more efficient in just over a year.
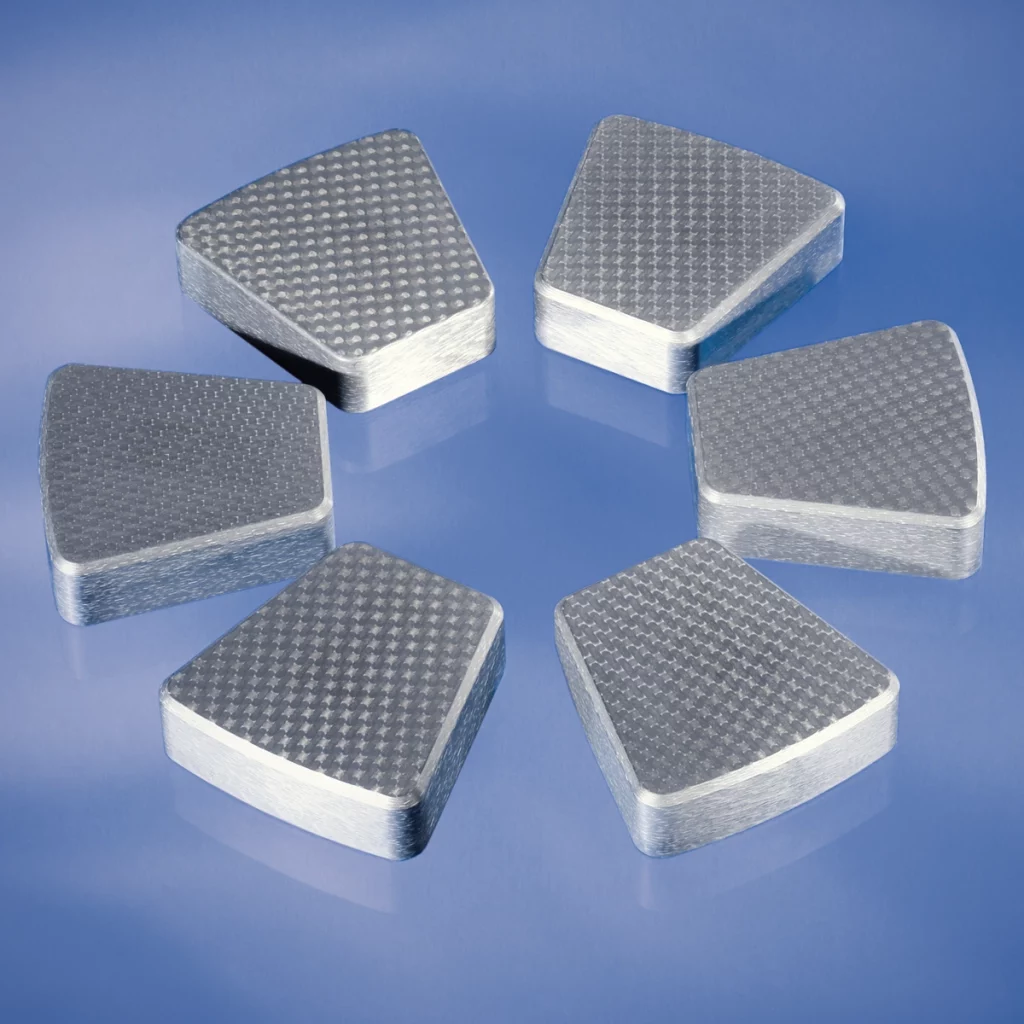
WR® 300/525/575 Materials
Three Materials in One Application
A top OEM customer in the U.K. needed to remove asbestos bearing materials in the Hayward Tyler wet wound motor boiler feed pumps in a coal-fired power plant.
To solve this, we used three different WR® materials in three different areas. WR® 525 sleeve bearings, WR® 300 thrust pads, and WR® 575 thrust pads brought together a powerful solution:
- Reliability & Increased MTBF – WR® materials increased MTBF from 4 to 9 years. That's more than double the run time with zero faults and continuous smooth operation.
- Regulatory Compliance – Pump lifetime increased while complying with environmental regulations.