PEEK vs PEK vs PTFE
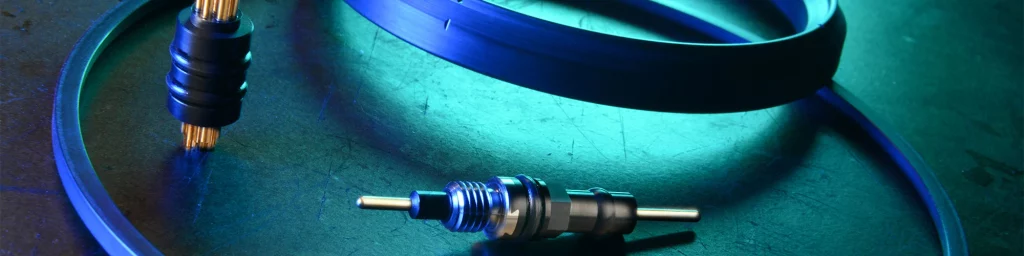
WHAT IS PEEK MATERIAL?
PEEK (polyetheretherketone) is a semi-crystalline thermoplastic with outstanding chemical resistance and mechanical strength across a broad temperature range, low moisture uptake, solid fire performance, and good dimensional stability.
PEEK plastic is strong and rigid with superior creep resistance, and delivers where thermal, chemical, and combustion properties are critical. PEEK material retains its properties in harsh high-pressure and high-temperature (HPHT) environments. Arlon 3000XT®, Greene Tweed’s proprietary cross-linked PEEK, has proven creep and extrusion resistance at temperatures above 350˚F (177˚C).
As constant innovators, Greene Tweed was the first company to use PEEK material in several oilfield applications. PEEK is often used as the body for electrical connectors to minimize thermal expansion, provide chemical resistance, and to promote effective sealing. Greene Tweed also uses PEEK materials for a variety of sealing system components, sensor housings, aircraft engines, and other demanding environments.
WHAT IS PEK?
PEK (polyetherketone) is a ketone-based, semi-crystalline thermoplastic. PEK delivers high thermal dimensional stability, low flammability, outstanding chemical resistance, and excellent mechanical properties over a wide temperature range.
Because PEK retains its strength as temperatures rise, it is ideal for applications with vibrational or cyclic loading conditions and where components must withstand high mechanical loads at high temperatures for extended periods of time, such as gears, shafts, bushes, bearings, and miniature rotational precision parts in the aerospace and automotive industries.
PEK retains its properties at temperatures up to 30˚C higher than traditional PEEK materials. Combined with good creep and fatigue resistance, PEK provides a property set uncommon in most polymers.
Like PEEK, PEK is also often used as the body for electrical connectors to minimize thermal expansion and provide effective sealing and chemical resistance.
WHAT IS PTFE?
PTFE (polytetrafluoroethylene) belongs to the fluoropolymer family, separate from poly ether ketones. Fluorine provides additional chemical resistance, especially to strong acids, and a low coefficient of friction, low moisture absorption, and high electrical resistance. PTFE is not as strong as other polymers, but more flexible at low temperatures. PTFE is stable at up to 500˚F (260˚C)
PTFE is used in back-up rings and as a component of specialty seals across a wide range of markets. PTFE is also used for low friction bearing components and electrical insulation or isolation. High purity grades are used extensively in fluid handling systems in the semiconductor market.
WHAT IS ARLON 3000XT®?
A proven performer, Greene Tweed’s Arlon 3000XT® is a non-filled, cross-linked thermoplastic material that delivers the benefits of conventional PEEK and PEK polymers while providing extended mechanical, electrical, and creep performance at high temperatures above 300˚F (150˚C).
Arlon 3000XT®’s provides superior electrical resistivity properties and reliability in high-temperature environments, safeguarding mission-critical operations in the most severe applications. When it comes to high-temperature and high-voltage applications, Arlon 3000XT® far exceeds traditional PEEK and PEK solutions.
Factory tested: Arlon 3000XT® delivers proven performance with 100 times the electrical resistivity of PEEK and 30 times that of PEK at temperatures of 400˚F and above. At room temperature, Arlon 3000XT® has extended capabilities above 20kV.
Download our PTFE vs PEK vs PEEK vs ARLON 3000XT® comparison table:
PEEK vs PEK vs PTFE
Let’s connect to see how PEEK ,PEK, or PTFE can support your business goals.
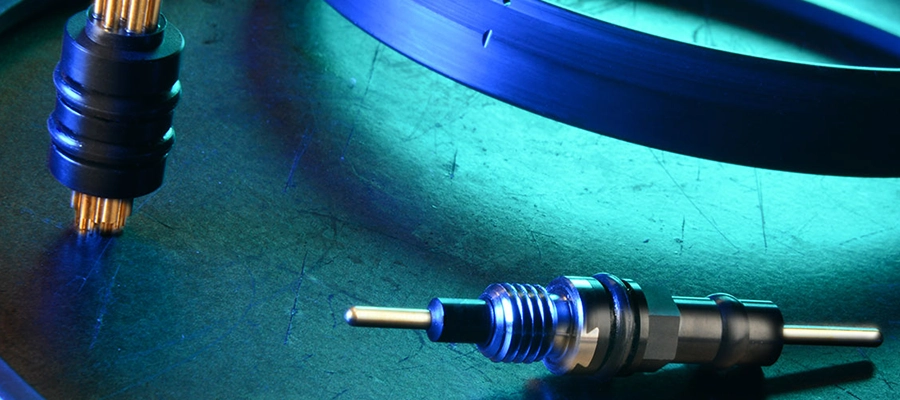