Get Your Components Ready: Hydrogen is All Set to Take Off
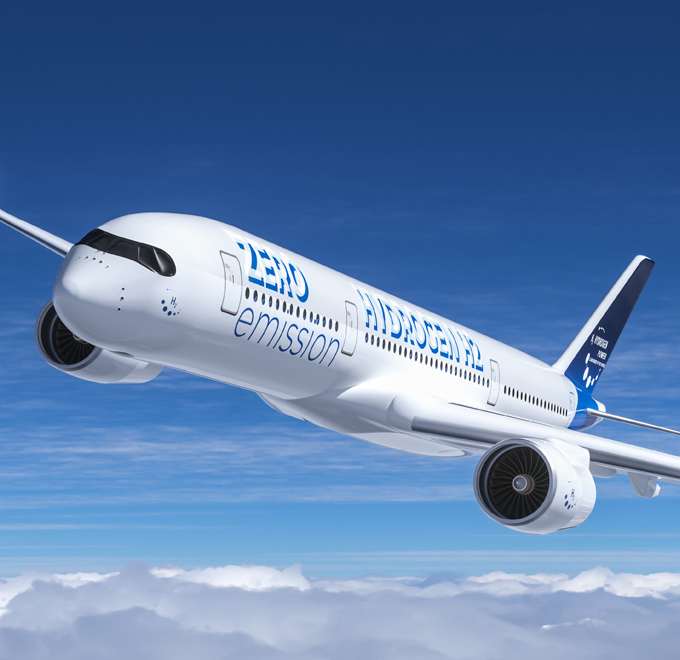
As we head into 2023, everyone in the aviation industry, from airline associations to intergovernmental organizations, is committed to making flying greener. For instance, the International Civil Aviation Organization (ICAO)1 and International Air Transport Association (IATA)2 have agreed to an ambitious goal of replacing all jet fuels with sustainable alternatives by 2050, thereby, drastically lowering emissions of planet-warming gases from airplanes.
As the push for carbon neutrality by 2050 ramps up, momentum is building up for sustainable aviation fuels. Hydrogen is emerging as a key contender in the quest to reduce carbon dioxide (CO2) being released into the atmosphere. US-based startup, ZeroAvia4, is all set to begin the test flight of its 19-seat Dornier 228 hydrogen fuel cell-powered aircraft this year. Several large aircraft manufacturers are getting serious about hydrogen-powered planes and large commercial aircraft are expected to enter the market in 2030 and scale up through 20505.
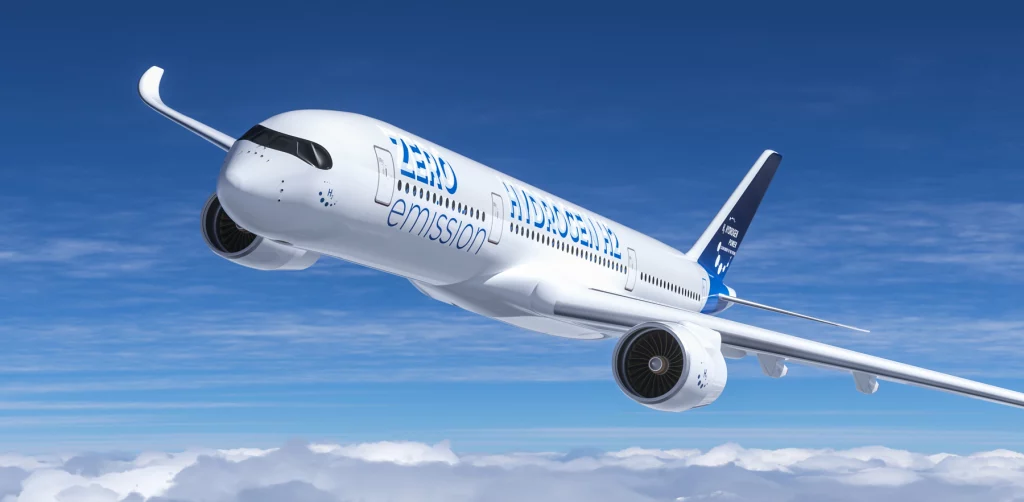
In a perfect world, aircraft would simply be fueled with hydrogen instead of the conventional Jet A fuel used today. The unfortunate reality is producing, storing, and transporting this next-generation, emission-free fuel comes with its own set of challenges. Some of the biggest challenges presented by the tiniest, lightest molecule known to man include:
Permeation
Hydrogen is an exceptionally light, low-density gas and can penetrate any type of polymer material, causing sealing issues and metal embrittlement. Depending on the pressure and temperature levels, Greene, Tweed recommends Fusion® 938 O-rings made from high-performance FKM or MSE® (Metal Spring Energized) PTFE lip seals. Fusion® 938 offers exceptional resistance to hydrogen exposure. For permeation issues at low temperatures, Fusion® 665 O-rings (FKM) or MSE® lip seals could be a solution of choice.
Lubricity
The low lubricity of hydrogen molecules is a concern in equipment, like valves and compressors, generating excessive wear and friction issues. To overcome these problems, Greene, Tweed offers WR® 600, a PFA composite with unique dry-running properties, and Arlon 3000XT®, the only cross-linked PEEK available in the market.
Excessive Weight
As the energy density of hydrogen (by volume) is around three times lower than jet fuel, reservoir sizes must be dramatically increased to transport the same volume of energy with hydrogen as with jet fuel. Therefore, offering lightweight solutions for hydrogen aircraft is even more critical. Greene Tweed’s thermoplastic composite solution, Xycomp® is already extensively used in the aerospace industry as metal replacement.
We are actively testing our materials at several independent laboratories and the results so far show our materials and solutions are ready to support and empower hydrogen infrastructure.
As hydrogen is showing all signs of becoming a promising pathway to decarbonization, it is time to get your equipment ready to take on the challenges presented by hydrogen.
1 States adopt net-zero 2050 global aspirational goal for international flight operations
2 Our Commitment to Fly Net Zero by 2050
4 ZeroAvia Gets CAA Green Light for Next Phase of Hydrogen-Electric Test Flights
Decarbonizing the aviation sector: Making net zero aviation possible
You May Also Like: