When Chemistry Seals the Deal
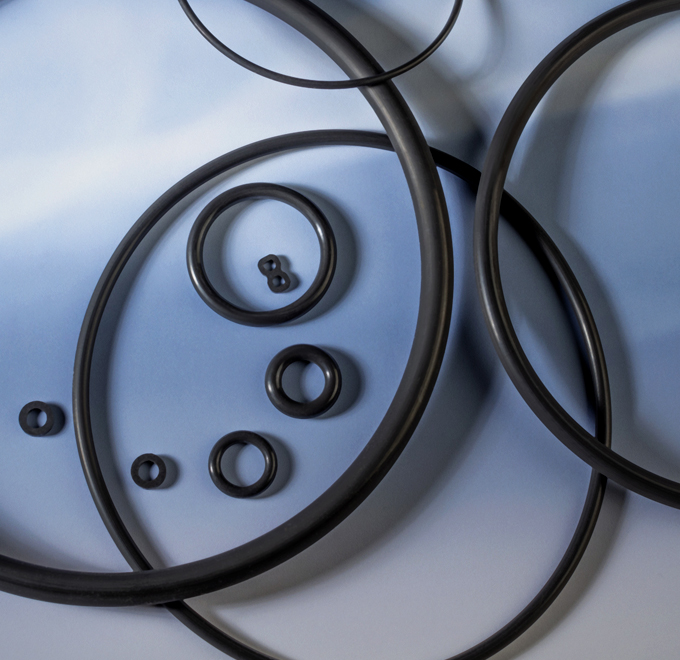
Selecting the right seal for your application is not easy. If you want reliable and long-lasting performance, it’s crucial to consider the following operational conditions.
- Service Pressure: High pressure applications require higher durometer o-rings to resist extrusion.
- Service Temperature: Different elastomers have different low- and high-temperature capabilities.
- Installation Parameters: Different elastomers have different elongation capabilities.
- Static or Dynamic Service: Each type of service may require a different elastomer and/or seal design.
- Service Media: Media incompatibility can cause swelling, hardness change, and physical property deterioration.
Greene Tweed’s applications engineering team will consider all these factors to make a recommendation on material and design. To assist with determining material compatibility with the service media, Greene Tweed has published guides for Chemraz® and its other materials on its website that provide good guidance on what material will work best in a particular fluid, including the nuances of the interaction of temperature on chemical resistance.

Greene Tweed’s chemical resistance guides are based on an evaluation of how material properties change in an immersion test. The immersion test is typically performed in-house in Greene Tweed’s ISO 17025:2017 accredited test labs and/or with third-party certified labs. The screening protocol provides an idea of how a particular material will perform in representative fluids. An applications engineer can analyze that data along with other application details, to recommend which material would best fit an application.
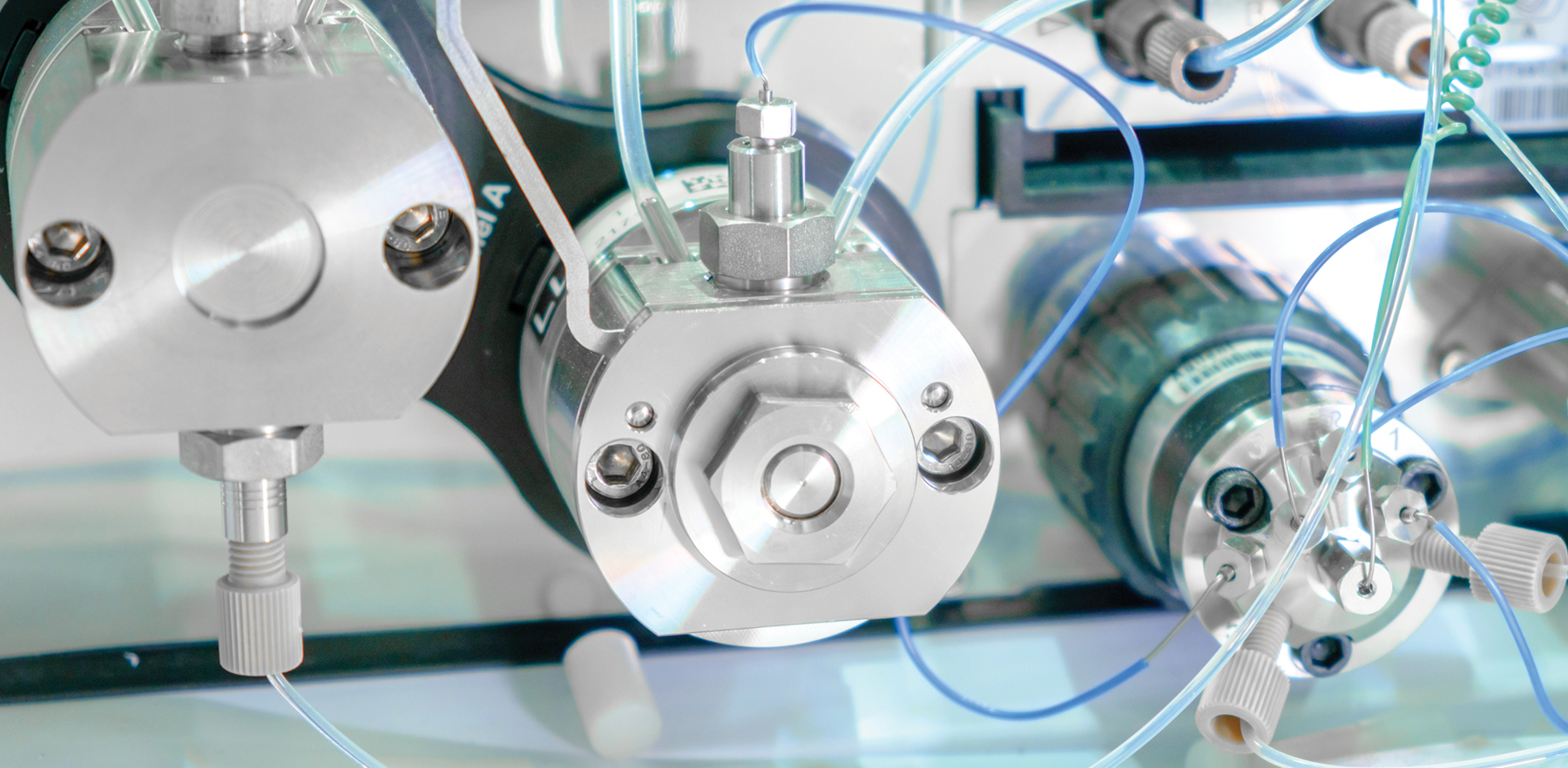
A midstream oil & gas customer, located on the Gulf Coast, recently contacted Greene Tweed looking for a material that could withstand its gas sweetening process which included an amine solution. To provide the proper material recommendation, Greene Tweed’s applications engineering team conducted a complete evaluation. The temperature of the fluid pointed to several Chemraz® compounds. Next, the team looked at chemical resistance. The examination indicated that a brand new Chemraz® compound, 541, could meet the customer’s requirements.
Chemraz® 541 was engineered as a universal purpose compound with utility across multiple markets including chemical processing, life sciences, oil & gas, and semiconductors. Chemraz® 541 seals have been installed in various applications including analytical instrumentation, gas sweetening, and mechanical seals. Given that Chemraz® 541 is designed to operate in a wide range of operational environments, establishing its chemical resistance in a variety of fluids was vital.
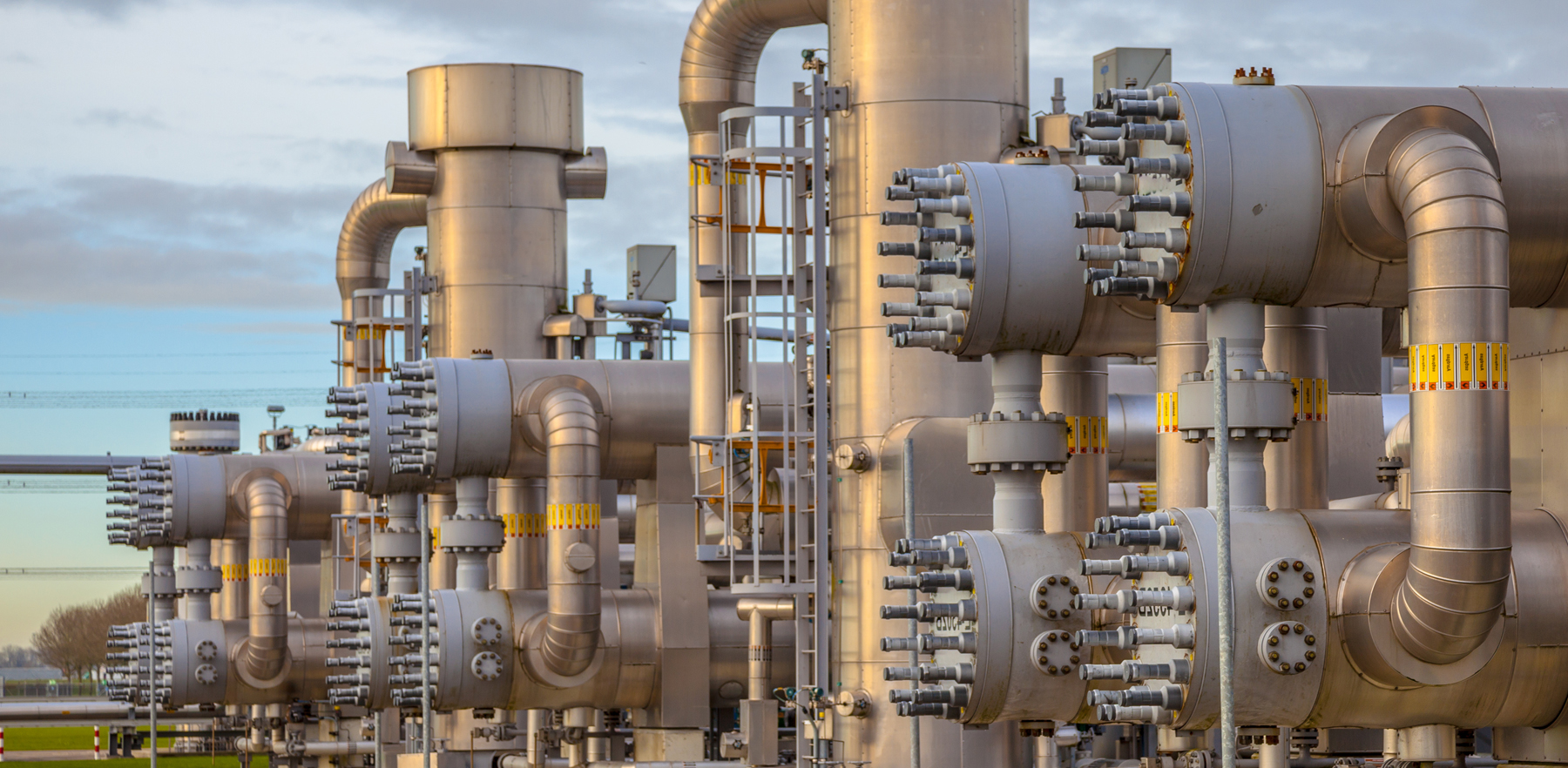
The chemical resistance testing protocol for Chemraz® 541 began with relatively benign fluids such as the Mobile Jet Oil II at an elevated temperature of 347° F/175° C for three days. Other fluids tested included distilled water and steam. The protocol then extends to an extremely aggressive test for acids and amines. Greene Tweed evaluates resistance typically based on immersion in sulfuric acid at 250°F/120°C for one week and amines compatibility is established by using diglycolamine at 302° F/150° C for the same period. As with standard immersion tests, measurements were taken before and after the fluid exposure.
Since the customer’s application required resistance to amines, Greene Tweed engineers included that attribute as a key performance differentiator to establish whether Chemraz® 541 could be a candidate. Greene Tweed evaluated the change in volume and tensile strength after the soak in digylcolamine to establish a rating for Chemraz® 541 and determined that since the material registered less than a 15 percent change, Chemraz® 541 exhibits excellent resistance to amines. After reviewing the data, the customer accepted and installed Chemraz® 541 o-rings in its application. The customer later reported back that the material was performing successfully and was living up to its designation as a “universal purpose” compound.