Fuel Pumps and Valves in the New Hydrogen Economy
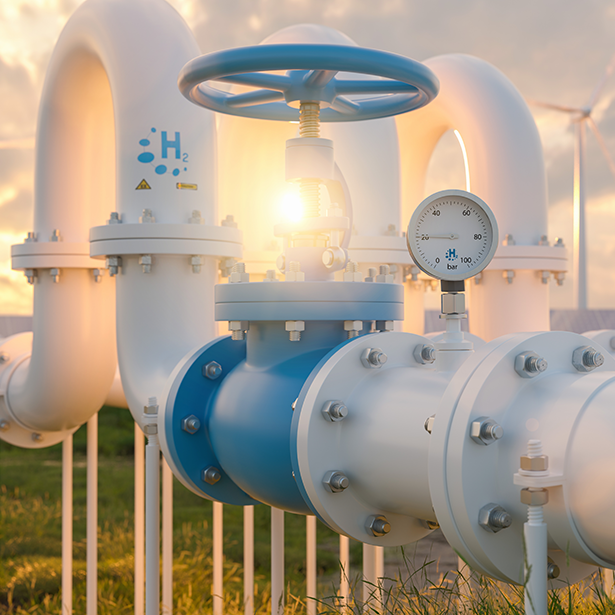
What is the future of pumps, valves, and turbomachinery, especially in supporting the Hydrogen economy and carbon capture plants? The question set off an insightful exchange of ideas and viewpoints among industry leaders from Greene Tweed, Baker Hughes, Cryostar, and FS-Elliott just published in Hydrocarbon Engineering, a leading publication covering the global refining, gas processing, and petrochemical industry.
The five-page feature called ‘Pumps, Valves & TurboMachinery Q&A’ featured insights and perspectives from Greene Tweed’s industry expansion manager, Philippe Allienne, who is responsible for business development for a portfolio of innovative material solutions targeted at the hydrogen and CCUS markets. While discussing recent challenging projects, Philippe acknowledged that hydrogen molecule’s interaction with materials and polymers is not yet well understood. “To overcome the challenges of finding a suitable testing procedure for materials in hydrogen service, we conducted intense global research and identified an advanced research program led by two major national labs and sponsored by the US Department of Energy (DOE), where we tested several of our materials under severe test conditions, with promising results.
During the interview, he took a moment to highlight Arlon®3000XT – the world’s first and only cross-linked PEEK-based polymer developed in 2014 by Greene Tweed – that enabled oil and gas companies to move to deeper reserves with increasingly higher temperatures and pressures. “It has since been used to extend the performance envelope, lifetime, and reliability of a variety of applications where PEEK or other extreme-performance plastics may not be sufficient. Recent testing has shown excellent high-temperature dielectric properties, enhanced creep resistance at moderate temperatures, and high elongation under cryogenic conditions, making it ideal for many hydrocarbon processing and hydrogen applications,” he said.

Discussing the role of pumps, valves, and compressors in the Carbon Capture, Utilization, and Storage (CCUS) process, he says, “Just like hydrogen they [CCUS process] require special attention and should be adapted to the specific needs of carbon dioxide (CO2) molecules. For example, rapid gas decompression (RGD) could represent a major problem in supercritical CO2 applications, primarily in the transportation phase. Special elastomers are required in equipment such as valves, compressors, or pigs found in these applications. Similarly, non-galling and non-seizing materials such as PEEK composites should be considered for pump wear parts in compression or injection applications due to the very low lubricity or supercritical CO2.”

When asked about Greene Tweed’s approach to equipment reliability and maintenance, he highlighted our composite parts. “At Greene Tweed, we are committed to developing materials and solutions that improve the reliability of critical equipment, including compressors, pumps, and valves. Take our composite parts, for instance. Customers who upgrade to composite wear parts from metal wear parts in their pumps experience reliability improvements and reported improved mean time between repairs (MTBR), minimized chance of catastrophic damage, reduced vibration, improved efficiency, and reduced total cost of ownership for the equipment.

Click here to read the full Q&A [Free subscription to the Hydrocarbon Engineering Magazine may be required]