Importance of FEA in Seal Design
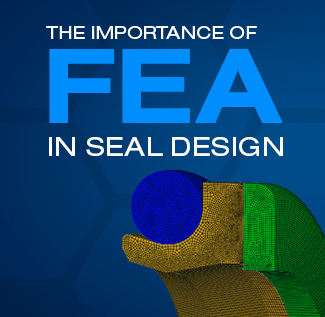
Seals are critical components of pressurized systems. The trend within all industries pushes the application conditions and, in turn, the seal performance, to the extreme.
Designing seals for these applications is quite challenging. Temperatures can exceed 500°F (266°C) in energy applications and plunge below -60°F (-51°C) in aerospace applications. Pressures can range from 3-5 ksi (20.7-34.4 MPa) in aerospace hydraulic systems to upwards of 40 ksi (275.7 MPa) in oilfield drilling. In addition, fluids can be corrosive and dynamic motion can be significant.
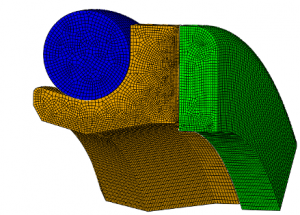
One of the engineering tools used in the seal design process is Finite Element Analysis (FEA). FEA is a numerical solution technique that can be used to simulate and predict the seal response under specific application conditions.
FEA can be utilized in seal design in several ways. The most common method is to assess the contact pressure profile. The contact pressure is the amount of pressure that a seal generates against the metallic hardware to resist the bypass of system pressure. The seal contact pressure will change based on the seal temperature, the amount of seal squeeze, and the applied system pressure.
This information enables designers to achieve sufficient contact pressure and length at all the temperature/pressure conditions of interest. Contact pressure and total contact force can also be used to compare multiple designs to determine the best design for any application.
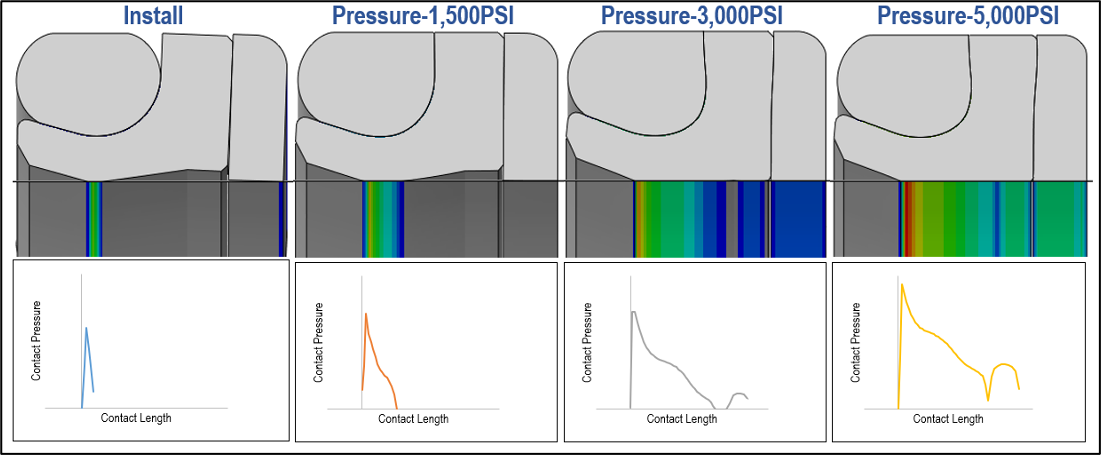
FEA is one of the many tools that enables Greene Tweed’s success in some of the world’s most challenging sealing applications.
Greene Tweed products are sold and distributed worldwide. Click here to contact us for additional information on our seal capabilities.