Greene Tweed Innovation Award Winner Spotlight: Dan King – Accelerating Product Journey
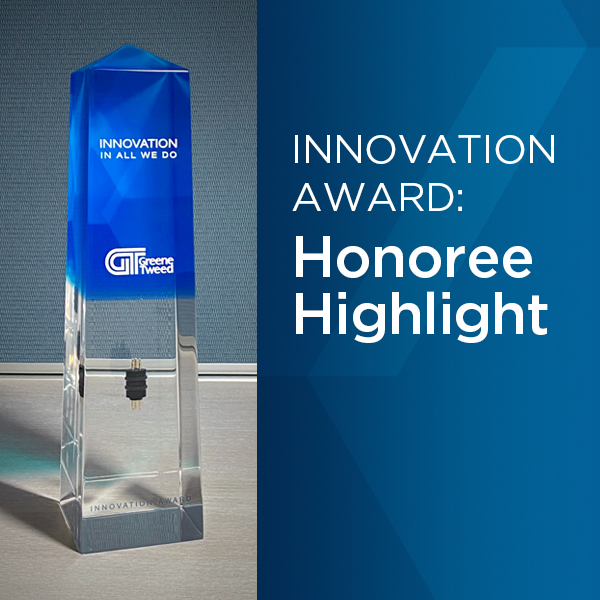
Meet Dan King, who led the development of the largest injection molded parts ever made with Greene Tweed’s Arlon 3000XT®, the world’s first commercialized crosslinked PEEK composite polymer. What sets his accomplishment apart is not just the innovative product that meets customers’ needs but also the remarkable speed at which it was brought to life – half the usual time frame. A research engineer in the Advanced Technology Group of Greene Tweed, he leveraged his technical acumen as well as entrepreneurial spirit, from identifying the need and procuring the material to designing the tool and making the first set of parts that will go into hydrogen service.
Recognizing his outstanding achievement, Greene Tweed honored him with our prestigious Innovation Award, which spotlights and rewards exceptional efforts to push the boundaries of innovation and collaboration. Hot on the trail of the special event where the award was presented by Chairman Allon Bloch, CEO Magen Buterbaugh, and COO Justine Franchina, we sat down with Dan to learn more about his journey of innovation, from conception to creation.
Congratulations on the Innovation Award! Tell us about Arlon 3000XT® and your work on it that led to this recognition.
Arlon 3000XT® platform is an incredible high-temperature cross-linked thermoplastic PEEK pushing the envelope of what is considered an “engineering material.” As a crosslinked PEEK, it offers considerable advantages over other PEEK grades due to excellent high-temperature properties and chemical resistance. It only makes sense that adding fillers to this material can enhance the properties even further.
Since I joined Greene Tweed five years ago, I have spent most of my time learning the intricacies of this material platform, optimizing, and improving properties to understand the correct way to process it. We saw a need for an enhanced glass-fiber Arlon 3000XT® material and I led a development effort to produce this new material. I applied my learnings from Arlon 3000XT® to guide the design an injection mold for a large plate — the largest part we’ve ever injection molded with any Arlon 3000XT® platform material. I advised mold-flow simulation to guide the development and finally was able to mold the first parts with this new tool, again applying my knowledge of the Arlon 3000XT® platform to produce both Arlon 3000XT® parts and parts of our experimental glass-filled grade. While we are still analyzing these parts, our initial results look incredibly promising.

We were able to identify the need, procure the material, design the tool, and make the first set of parts in half the typical time. Additionally, Greene Tweed has been able to provide samples of this new prototype material that has delighted our customers.
What does this award mean to you?
I thoroughly enjoy the development work I get to do when it comes to these new materials. The Arlon 3000XT® material platform is incredibly unique and with that comes some unique challenges in processing the material. To go from concept to prototype with a new, never-before-made grade of glass-filled Arlon 3000XT®, applying what I have learned about the material system ultimately leading to a successful prototype part of not only this experimental material but one of the largest injection-molded Arlon 3000XT® part Greene Tweed has made so far is incredibly gratifying. To be recognized for this work by Greene Tweed is certainly the icing on the cake.
What inspired you to develop the new material and the new process?
At Greene Tweed, we have unique customers with some very unique needs, and we felt that an enhanced glass-fiber grade was needed to meet the extreme requirements of their new and emerging applications. Arlon 3000XT® itself is an incredibly fascinating and powerful material, with exceptional properties that give it a strong advantage over standard PEEK. At the same time, it comes with some unique challenges that need to be overcome. Over my years at Greene Tweed, our Advanced Technology Group team and I have made significant strides in understanding the material and this knowledgebase was instrumental in being able to set up the mold and process to make these parts which are the largest injection-molded parts we have made to-date with any Arlon 3000XT® material.
Who else collaborated with you or supported you throughout this endeavor?
I’d like to acknowledge the entire Advanced Technology Group at Greene Tweed for their excellent hard work in making this material and technology the best it can be. I’d especially like to acknowledge Kerry Drake, ATG Plastics Technology Manager. Without his steadfast support and vision, this project would not have been possible. Thank you. I am truly humbled and honored to be a part of the team in a company that values innovation and continuous improvement as much as Greene Tweed.

How would you describe the impact of your innovation?
New and emerging technologies need new and emerging solutions. We have seen thus far that existing products can’t make the cut when it comes to some of these highly-demanding applications with extreme requirements. Greene Tweed has recognized that new materials are needed for these applications, and this work is the first step in the proliferation of Arlon 3000XT® as a material into an Arlon 3000XT® family of materials. These plates will be used for prototyping and will enable Greene Tweed to continue to fulfill our dedication to providing world-leading solutions for world-leading technologies.
What do you think is the path forward for the product you have pioneered?
Ultimately, I envision the commercialization of this material and greatly look forward to its commercial success. We will continue to improve the material and its products for the foreseeable future and the learnings made here will be applied to future growth of the Arlon 3000XT® platform with more engineered grades to meet specific needs.
