How Greene Tweed Restored Standard Lead Times for Semiconductor Customers
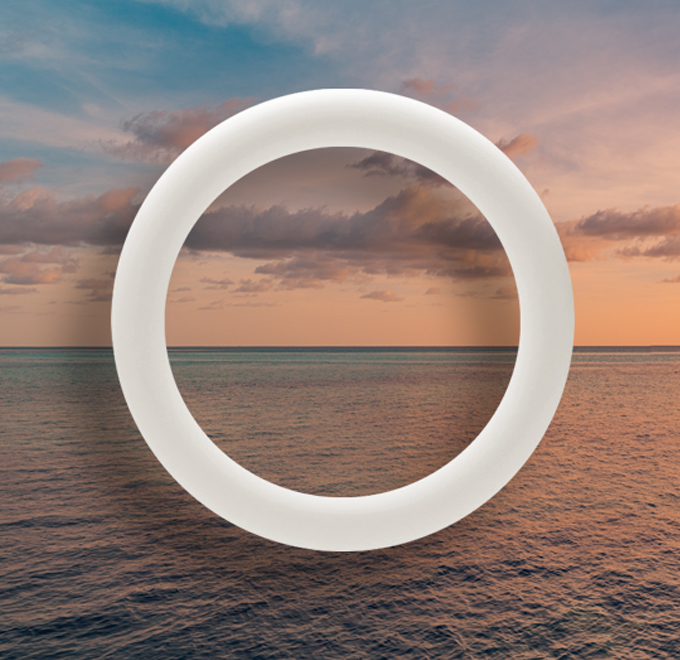
Over the past two years, semiconductor shortages have captured the world’s attention. But for those in the industry, this crunch also shed light on the vital importance of several small components that quietly power the chip manufacturing process but often go unnoticed.
One such component that drew significant attention last year was the Perfluoroelastomer (FFKM) seals. The high-performance FFKM elastomer material is critical for the most challenging semiconductor manufacturing applications since they help prevent contamination while withstanding aggressive chemicals and extremely high temperatures.
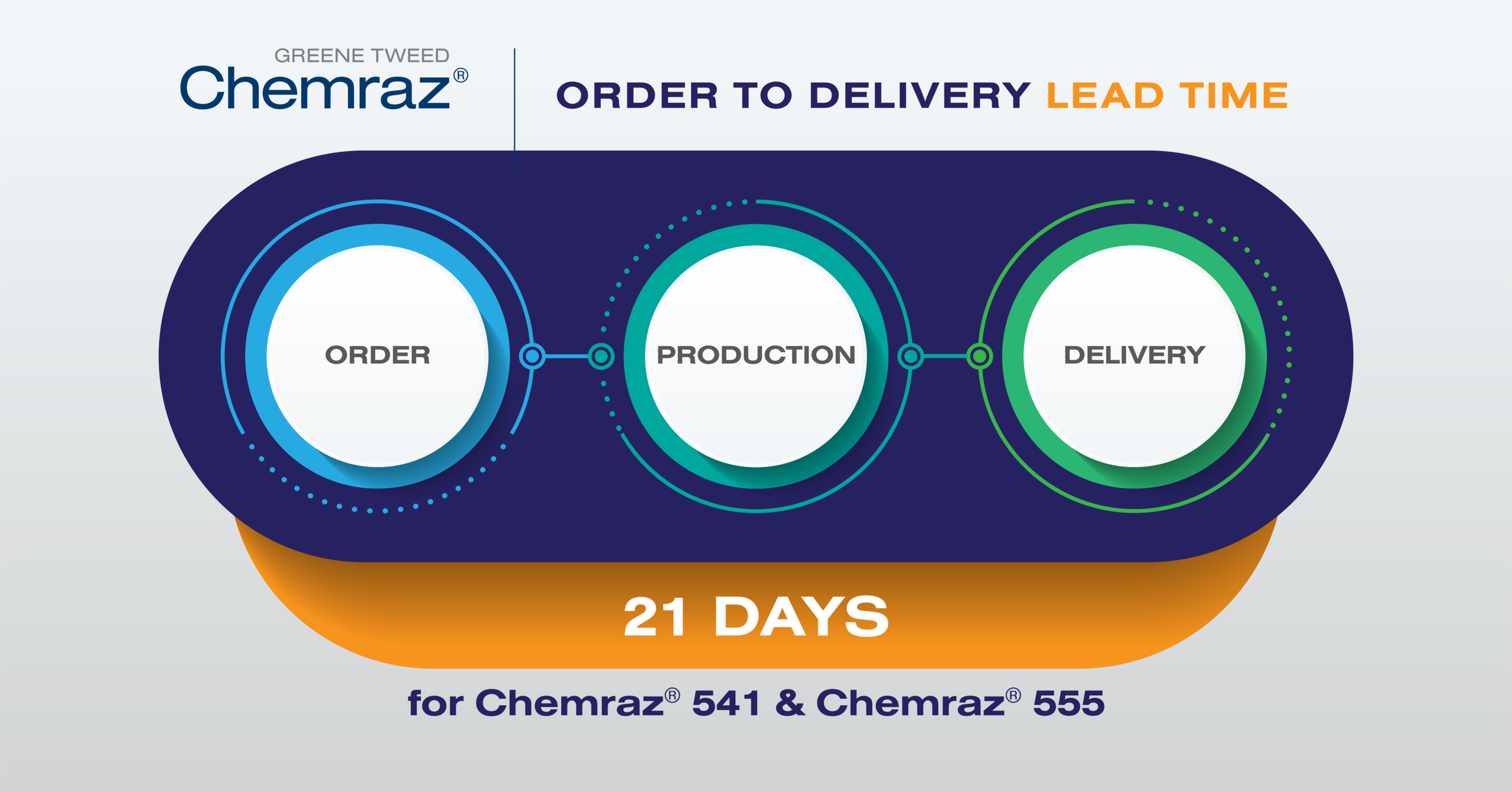
An unexpected and tumultuous supply crunch gripped the FFKM industry due to several factors, including pandemic lockdowns and geopolitical events such as the Russia-Ukraine war. The situation was exacerbated by an announcement from 3M, a major supplier, that it will stop producing all flouropolymers, fluorinated fluids, and PFAS-based additive products by the end of 2025. Unfortunately, the FFKM shortages coincided with a significant surge in demand for semiconductors. Soon, the FFKM industry found itself caught in the middle of a perfect storm.
As a global leader in seals based on elastomers such as FFKM, Greene Tweed decided to take action. “We saw the ripple effects of the shortage of FFKM seals and components and wanted to ensure that such disruptions wouldn’t compromise our customers’ ability to make chips,” says Thyag Sadasiwan, Director, Chemraz, at Greene Tweed, “While the semiconductor industry may be experiencing a downturn, predictions point towards an upturn in the second half of next year. In these uncertain times, even a downturn cannot eliminate the potential for supply disruptions leading to tightness and a resultant surge in demand. We are proactively taking measures to ensure a steady and uninterrupted supply.”
Realizing that the dynamic landscape of the semiconductor industry demands strategic planning and foresight, Greene Tweed has started building robust Business Continuity Plans (BCPs). “There’s a lot of uncertainty in the market. This forward-thinking mindset will empower us to swiftly react to these uncertainties and secure the supply we need to shield our customers,” Thyag explains.
He lays out Greene Tweed’s four major initiatives that will help circumvent future disruptions and secure a regular supply that will drive customers’ continued growth and success:
Secure FFKM Polymer Supply
The first step is to build strategic stockpiles of critical raw materials to prepare for the anticipated upturn. However, securing raw material is just one aspect of the multifaceted approach to ensure supply. Greene Tweed scientists are innovating to develop new products and reformulate existing ones to prepare for the ever-evolving regulations and shifting market dynamics. “We are continuously working with our supply chain partners to determine the potential impact of governmental reviews and supply crunch on their materials, chemicals, and production processes. Simultaneously, we work with our customers to develop and validate alternate compounds ahead of any changes,” explains Thyag.
Diversify Supply Chain
While reformulating and developing new products, Greene Tweed is taking proactive measures to diversify their supply chain to reduce the risk of overreliance on a single supplier or region. Thyag elucidates, “We realize that setting up multiple FFKM factories is too capital intensive and might not be feasible for our suppliers. That’s why we are leveraging multiple suppliers to build a resilient and adaptable supply chain that is better equipped to navigate the challenges of an ever-evolving semiconductor landscape.” He goes on to explain how Greene Tweed is carefully selecting compounds for equivalent products to strategically establish parallel supply chains. “We are developing equivalent products that serve as alternatives to the original ones. For example, we are augmenting our supply chain by adding Chemraz® G57 that is equivalent to Chemraz® 657. We source raw materials for two equivalent products from different suppliers located in separate countries.”
Expand Manufacturing Operations
That’s not all. Greene Tweed is also spreading its manufacturing footprint, strategically setting up factories in new locations across the world. Take the latest Korean manufacturing facility that will bring supply chain stability to the semiconductor customers in the region. Expected to be ready mid-next year, it will initially be dedicated to the Chemraz® product line, one of the most widely adopted and advanced FFKM elastomer seals that enable reliable performance and meet the most demanding specifications and standards of semiconductor manufacturing. “By decentralizing production and sourcing, we are better equipped to manage supply crunches, overcome production bottlenecks, and maintain consistent deliveries to customers,” he says.
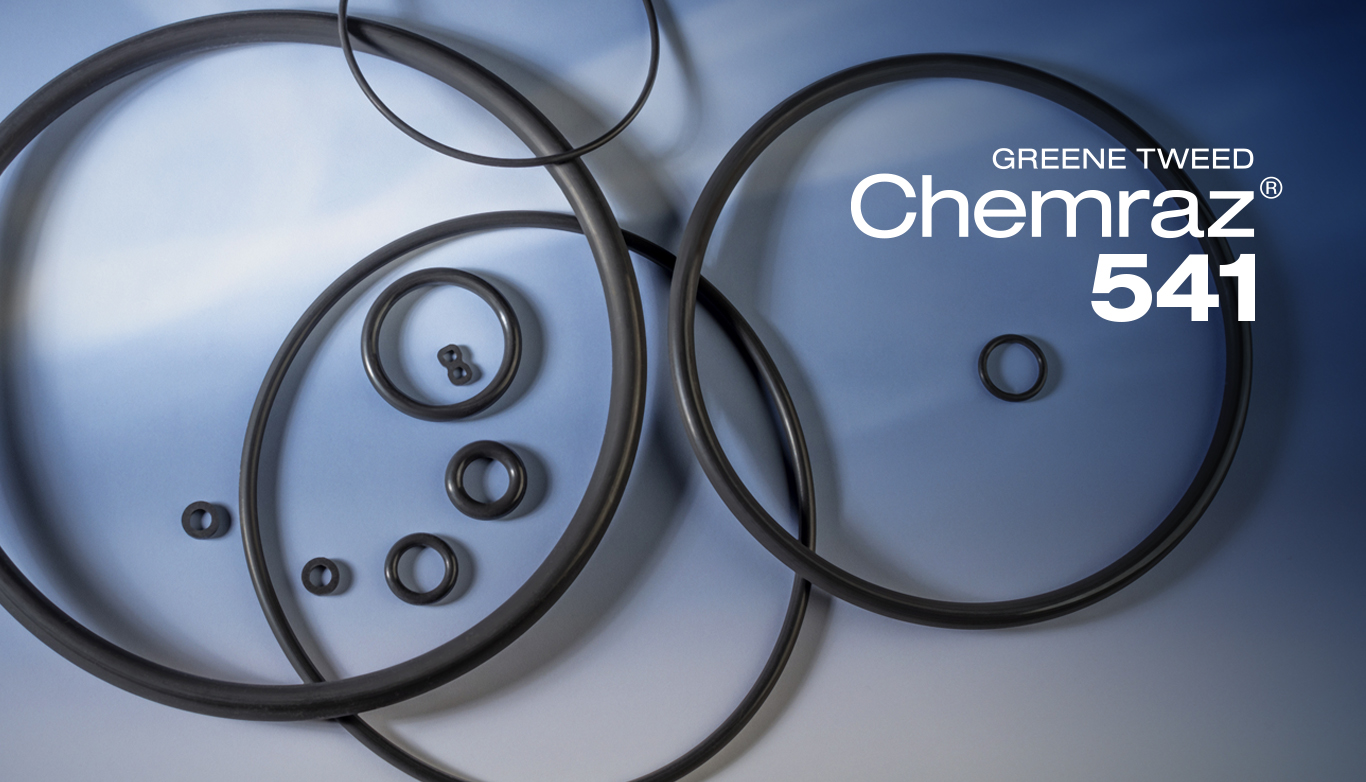
Boost Operational Capacity
In tandem with the expansion of manufacturing capacity, Greene Tweed has significantly stepped-up recruitment at its production floor. Thyag explains, “We are hiring to implement extended shifts and run seamless operations around the clock as required. Coupled with our new facility, this will help us grow our capacity and capability to better support the global demand for our products and bring enhanced supply chain stability to the semiconductor industry.”
Lead Times: Back on Track
The results of building supply resiliency are already evident. Greene Tweed has been able to restore standard lead times and offer a stable supply to the semiconductor industry. “We are back to pre-disruption lead times that our customers saw before geopolitical and regulatory events caused unprecedented supply chain issues – it’s a testament to our resilience, adaptability, and customer-centric approach,” Thyag concludes.