How to Ace the AMS 7410 Sealing Challenge
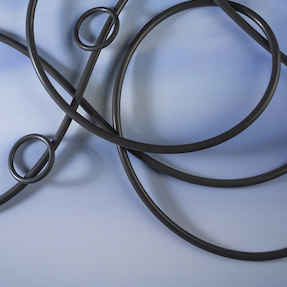
In the world of aviation, precision and perfection are paramount. Engineers meticulously scrutinize every component, from engines to landing gear. But what about seemingly small components such as elastomer seals?
Despite their size, the elastomer seals play a critical role in the safety and reliability of an aircraft’s hydraulic and fuel systems because they create a tight seal to prevent any leakage. However, when exposed to low temperatures, these seals can experience compression set, which is the permanent deformation of the material due to prolonged compression. This results in decreasing seal force and has the potential to create leaks over time, especially at low temperatures.
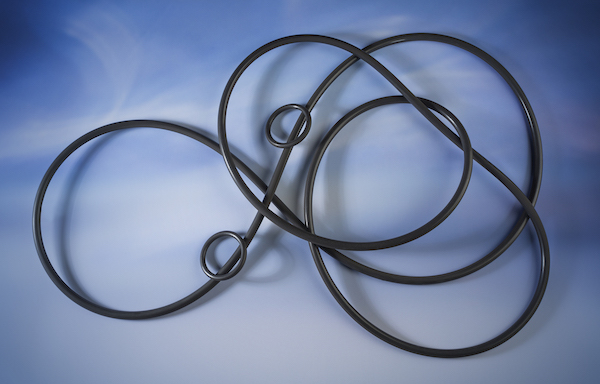
To combat this issue, the Aerospace Material Specification AMS7410 was developed. This specification outlines the requirements for elastomer seals to withstand compression set at low temperatures, ensuring the safety and reliability of aircraft systems in extreme conditions.
The Quest for the Ideal Seal Material
Choosing the right elastomer material is crucial for seals that can withstand compression set at low temperatures. The aviation industry has explored various options with Nitrile Rubber (NBR), Flourosilicone Rubber (FVMQ), and Fluoroelastomer (FKM) emerging as popular contenders. “Each material has its strengths and weaknesses but meeting the stringent requirements of AMS 7410 is no easy feat,” says Arturo Flores, product manager at Greene Tweed. According to him, NBR is a very common aerospace material that has good low temperature capabilities and good abrasion resistance, but it has high compression set at temperatures above 250°F (or 121°C). FVMQ provides better low-temperature performance but isn’t suitable for dynamic applications and is incompatible with lubricating oil. FKMs, known for their wide temperature range and chemical resistance, appears promising, but finding a specific FKM material that satisfies AMS 7410 can be challenging.
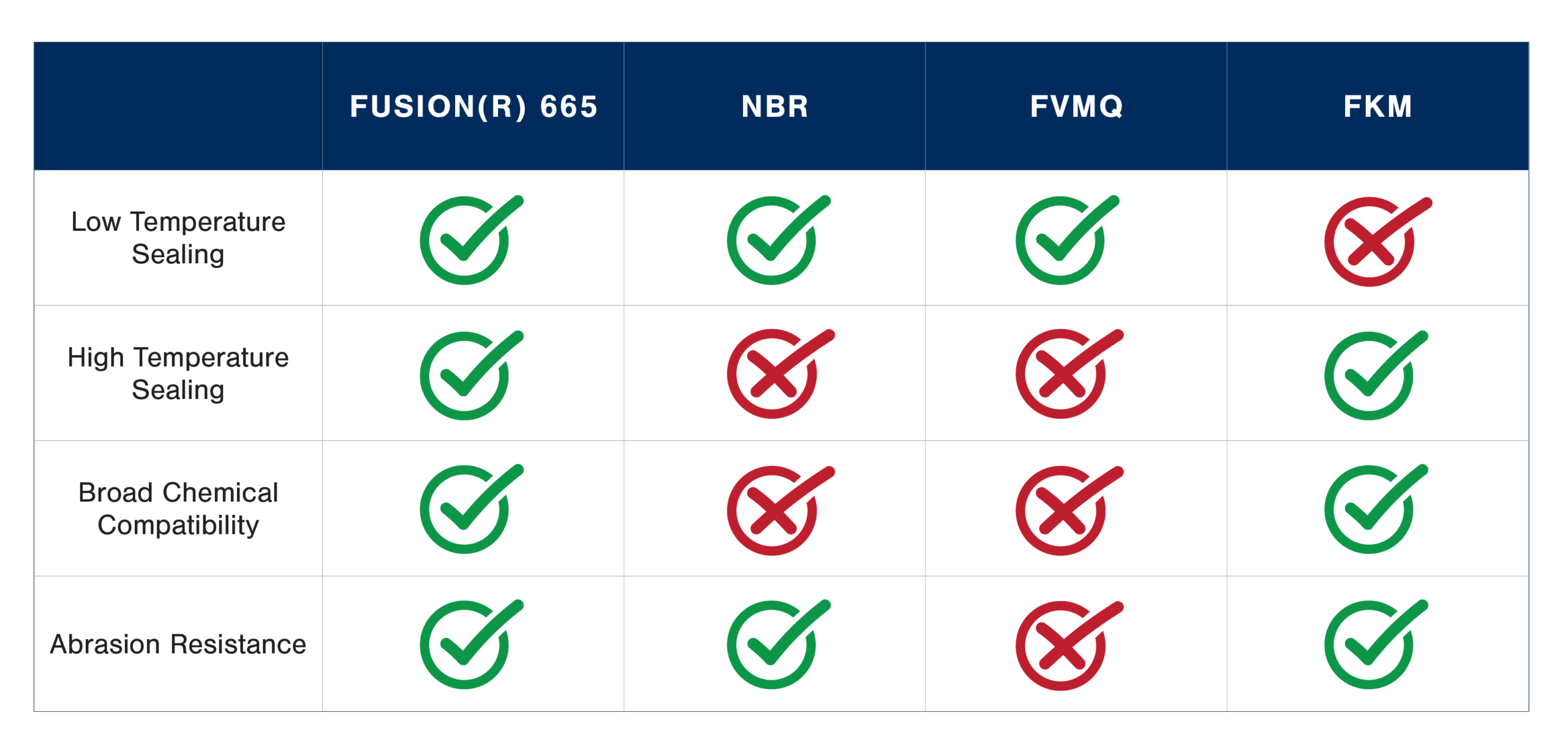
Soar High with Fusion 665
This quest for the right FKM material led Greene Tweed engineers to develop a seal material that not only withstands the frigid temperatures of high-altitude flights but also maintains its sealing capabilities under prolonged compression. Called Fusion® 665, the chemical-resistant elastomer performs well at both low temperatures (-70°F/ -57°C) and high temperatures (450°F/232°C). “It is specifically formulated to meet and exceed the requirements of AMS 7379 and AMS-P-83461, as well as the new AMS 7410. It has an extremely low compression set, broad chemical compatibility, and good abrasion resistance, thus overcoming the limitations of existing NBR, FKM, and FVMQ solutions,” explains Arturo.
Fusion® 665 has been rigorously tested and certified to meet AMS 7410. Compression set testing is used to determine the ability of elastomeric materials to maintain elastic properties after prolonged compressive stress. When tested for 70 hours at 275°F (135°C) in MIL-H-83282 per ASTM D395 Method B, Fusion® 665 compression set was measured at 9%, compared to NBR at 38%.
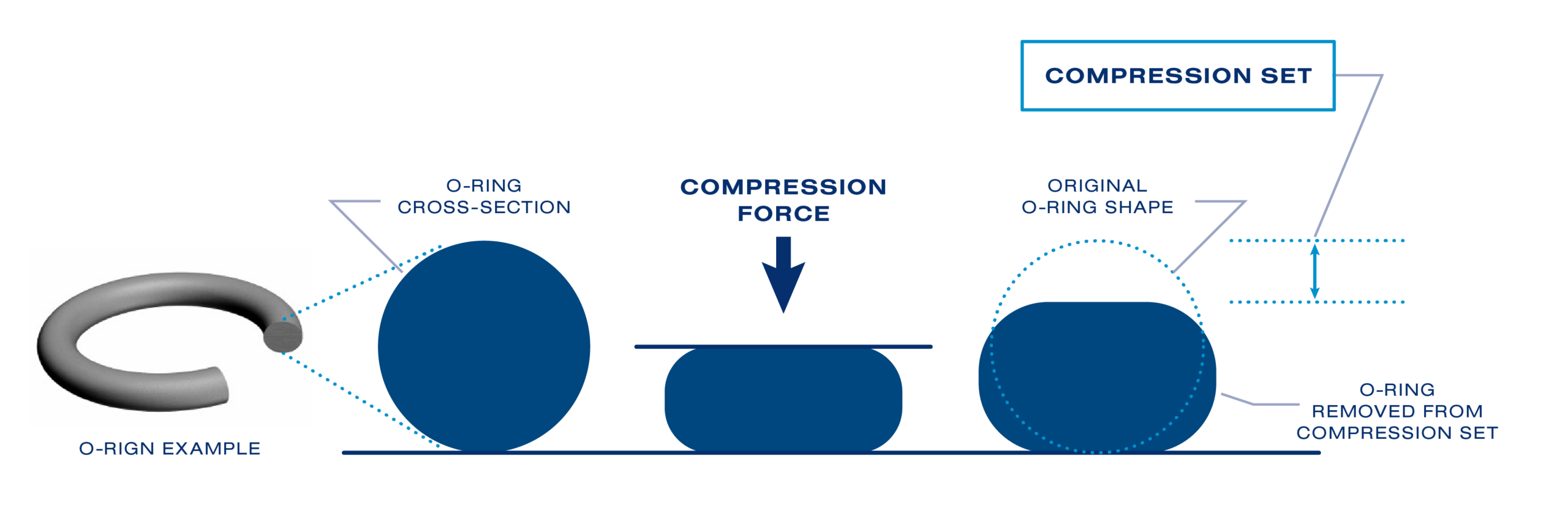
Besides O-rings, Fusion® 665 can be molded into proprietary seals, such as our AGT® Ring, CGT™ Capped GT Ring, Ener-Cap®, and ACT® Advanced Concept GT Ring seals.
So, if you’re in the market for elastomer seals that can withstand compression set at low temperatures and meet AMS 7410 specifications, contact Greene Tweed to explore what Fusion® 665 seals can do for your flight control and aircraft engine systems.
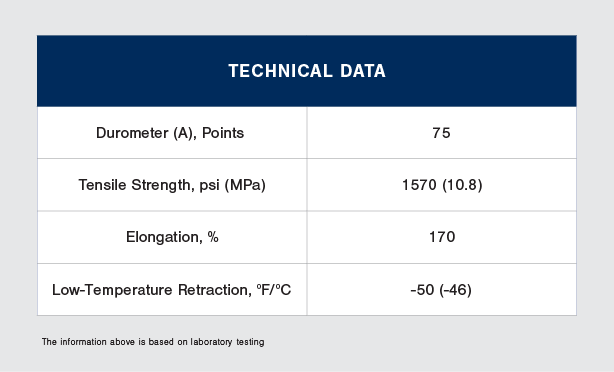