Why the Surface Finish of your Seal’s Mating Hardware Matters

What would you do if a sealing system on your semiconductor process equipment just failed prematurely or stopped functioning properly? Your first instinct would be to check if the seal is defective. The most often items on a seal failure checklist are chemistry, process pressure, and local temperature.
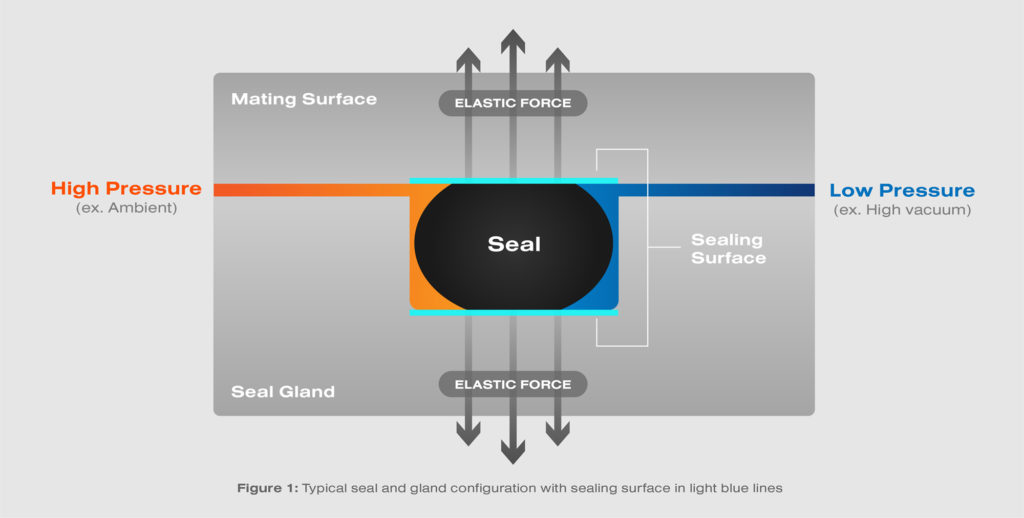
However, a few important items are missing from that list. These relate to the gland hardware and their corresponding surface roughness. Such subtle aspects of the hardware design could make or break a seal’s ability to function properly, and more specifically could impact the dynamic lifetime of a sealing element.
The term “surface finish” usually refers to the level of polishing or texturing applied to the surface of a part or component. Surface finish parameters can be described by three objective measurements of roughness, waviness, and lay. Roughness is usually composed of smaller irregularities, while the waviness consists of larger undulations. Lay refers to the direction of the dominant grain or texture on the surface. For the purposes of elastomer-based sealing products, roughness alone is often used to account for the finish, quantitatively. Various acronyms are used in describing surface roughness, including Ra, Rsk, Rq, Rku, Rz, RMS, etc. Micrometers or even microinches are the most common surface roughness, and smaller the number the finer the finish.
Surface finish requirements depend on whether the seal is elastomeric, thermoplastic, or another material. The overall malleability of elastomers allows for greater variation conformity in the surface finish. Although load (the weight applied to seal from system elements) and chamber pressure differential would often cause the soft, elastomeric material to conform to the gland’s textural constraints, too large roughness of static sealing products can create possible leak pathways for the media. Such leakages can, for instance, introduce ambient air into processes that are highly sensitive to water (as air moisture) and oxygen.
Below is a depiction of the localized variations in surface height and roughness that shows how surface roughness measurements are made in a general sense. It is easy to imagine that if there were too many of the peaks like the one towards the left of the diagram, seal materials would be abraded or worn away by dynamic contact, not to mention having trouble conforming to all the variability in localized surface height. Also, the valley towards the right of the image demonstrates how a pocket is formed, which could allow trapping of the particle contaminants or lubricant for decreasing the friction through continuous dynamic cycles.
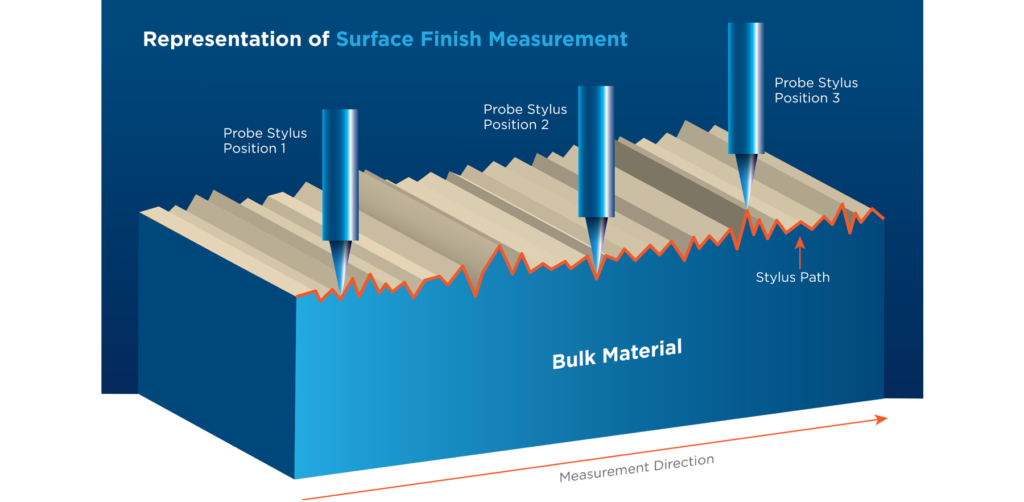
Choosing the right surface finish for the hardware components in your application can be complex. Generally, we recommend 8 to 12 microinches Ra (Average Roughness) for dynamic seals, and 16 to 32 microinches Ra for static seals. Greene Tweed’s experienced engineers can help you by accessing your application parameters to guide you to the right surface finish.
Additionally, surface finish requirements are different for applications that seal gases or vacuum than those required for sealing liquids. For gas sealing or sealing against a vacuum, a finer surface finish is recommended as the structure and size of most gasses allow them to pass through smaller gaps than a liquid would be able to move through.
While surface finish of seal glands is largely defined by “as machined” status, end users can and do impact the long-term condition. Specifically, when seals are removed from the gland and when the gland is cleaned prior to a new seal installation, these are opportunities to introduce roughness via hand tools use and cleaning protocols.
You May Also Like:
Three Tips to Extend your Seal’s Life in Semiconductor Applications